ARTICLES
Filters
View All
Keyword +
Market +
Requirement +
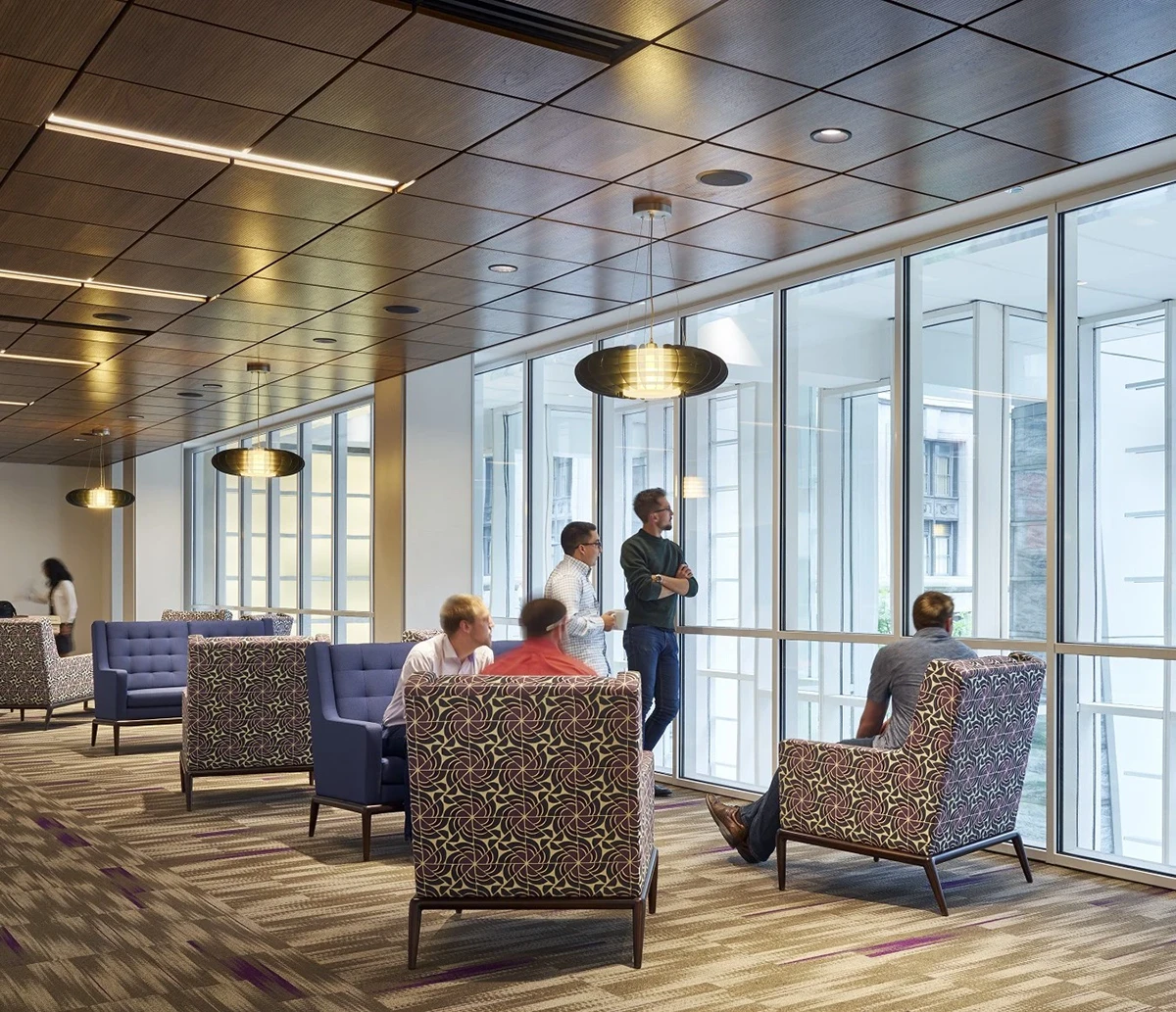
Balancing Life Safety and Security
Balancing Life Safety and Security
Date: Apr 2025
Publication: US Glass
>>
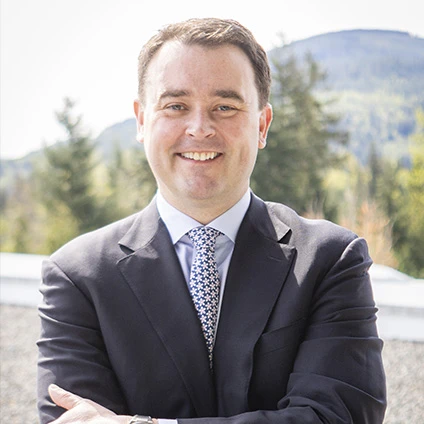
Faces: Devin Bowman
Faces: Devin Bowman
Date: Mar 2025
Publication: Door Security and Safety
>>
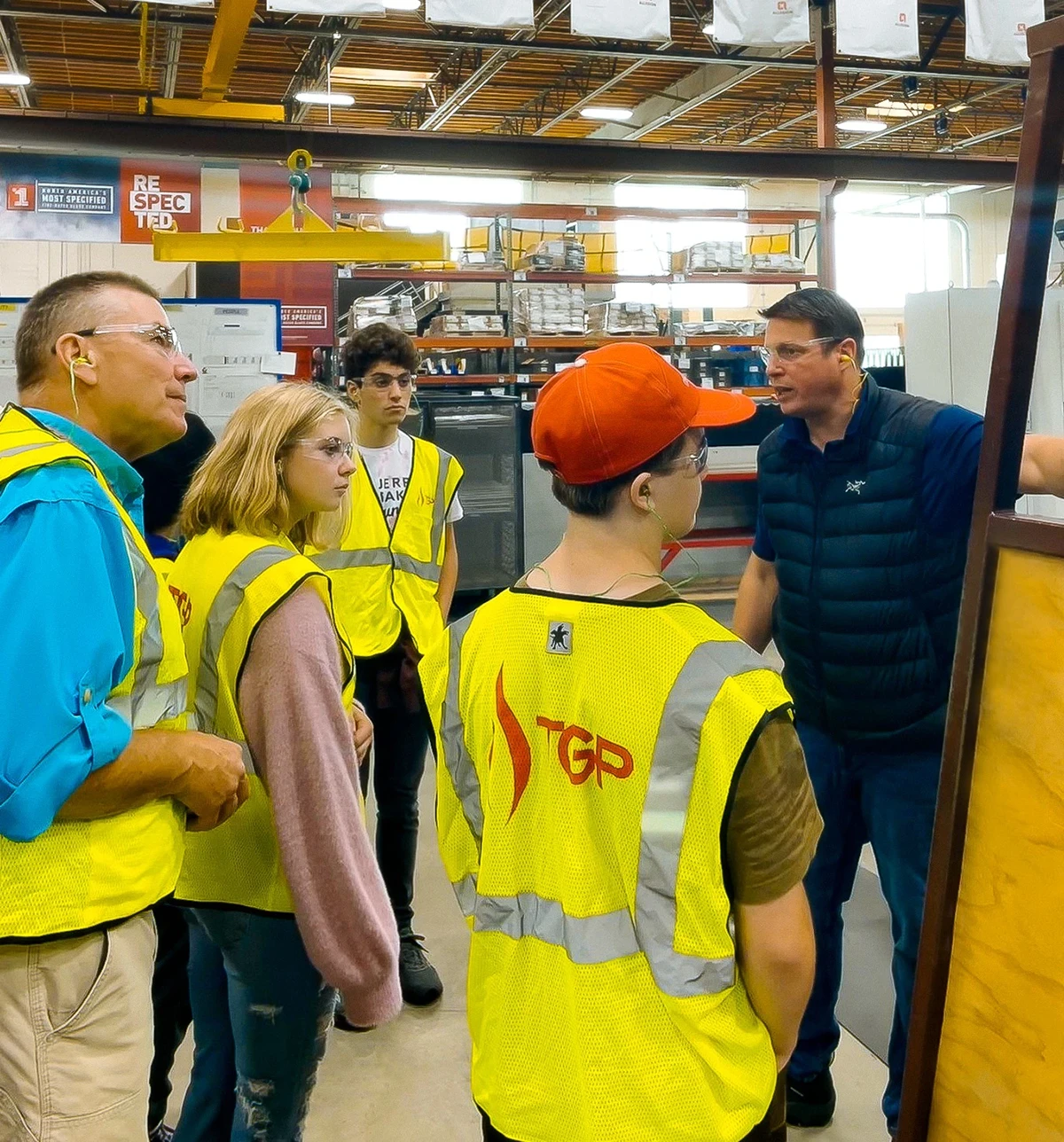
Opening the Door to the Next Generation
Opening the Door to the Next Generation
Date: Mar 2025
Publication: Door Security and Safety
>>
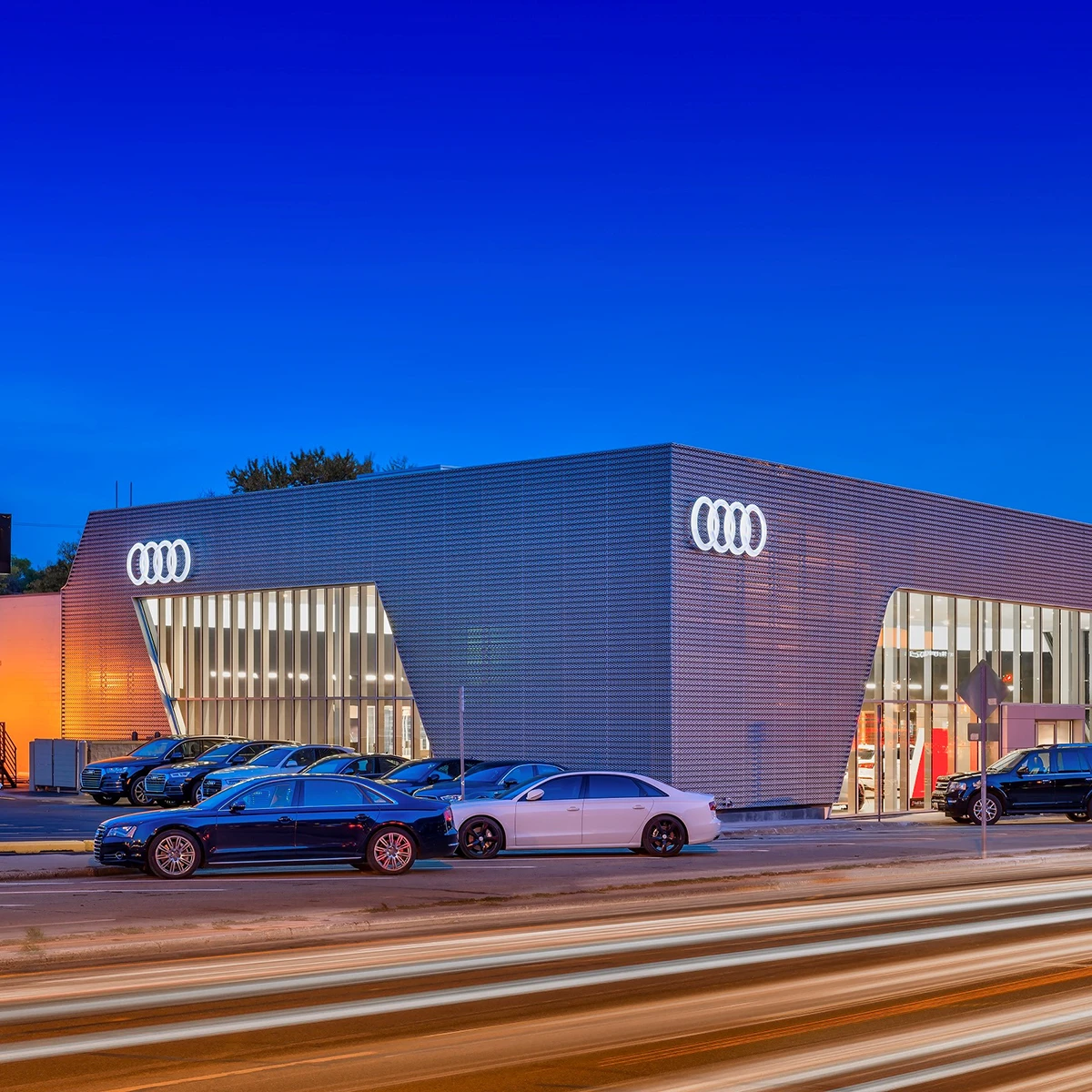
Achieving Transparency and Protection on the Façade with Fire-Rated Curtain Walls
Achieving Transparency and Protection on the Façade with Fire-Rated Curtain Walls
Date: Mar 2025
Publication: Building Enclosure
>>
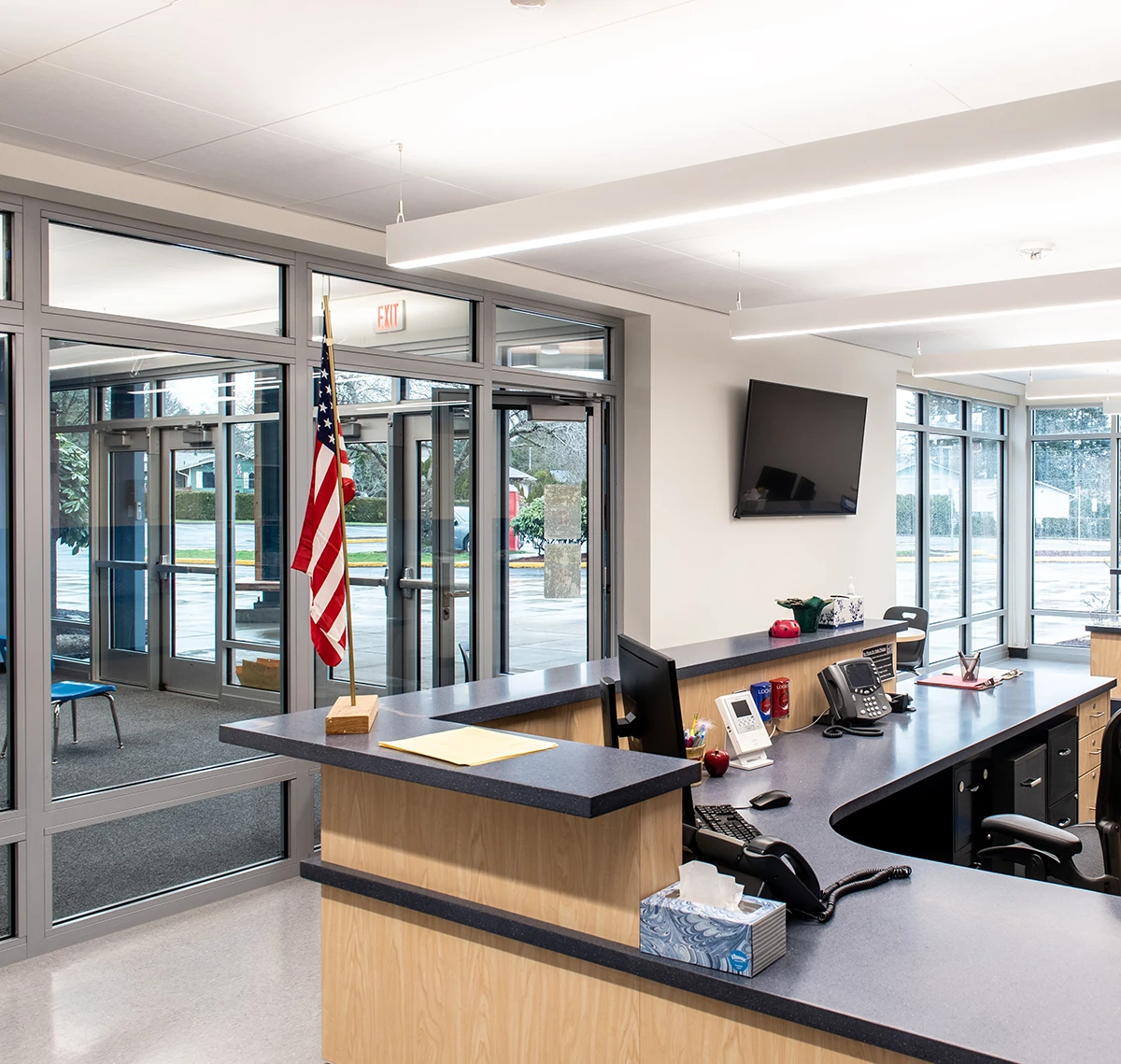
How the Glass Industry Aims to Improve Protection Against School Shootings
How the Glass Industry Aims to Improve Protection Against School Shootings
Date: Feb 2025
Publication: US Glass
>>
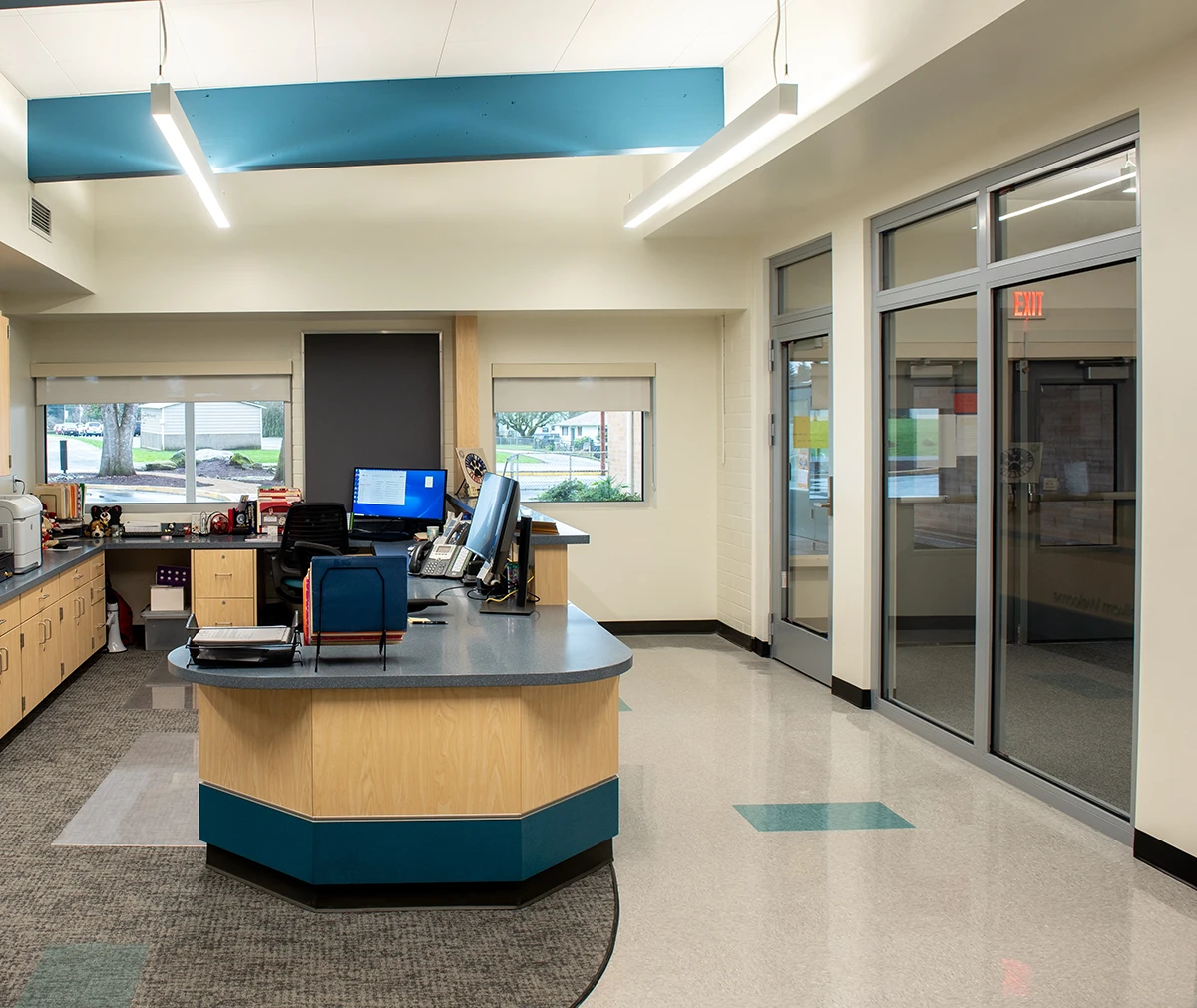
Achieving Code-Compliant School Security with Fire-Rated and Forced-Entry Resistant Glass
Achieving Code-Compliant School Security with Fire-Rated and Forced-Entry Resistant Glass
Date: Feb 2025
Publication: Campus Safety
>>
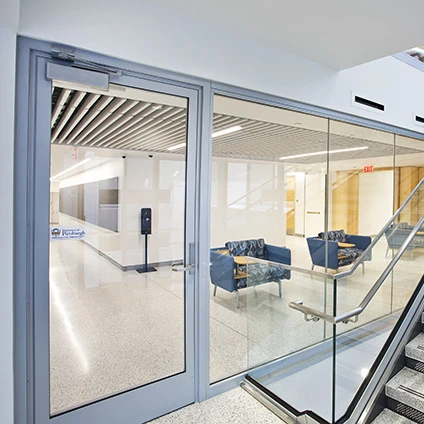
Demystifying Passive Fire Protection: Fire-Rated Glass and Retrofits
Demystifying Passive Fire Protection: Fire-Rated Glass and Retrofits
Date: Feb 2025
Publication: BUILDINGS
>>
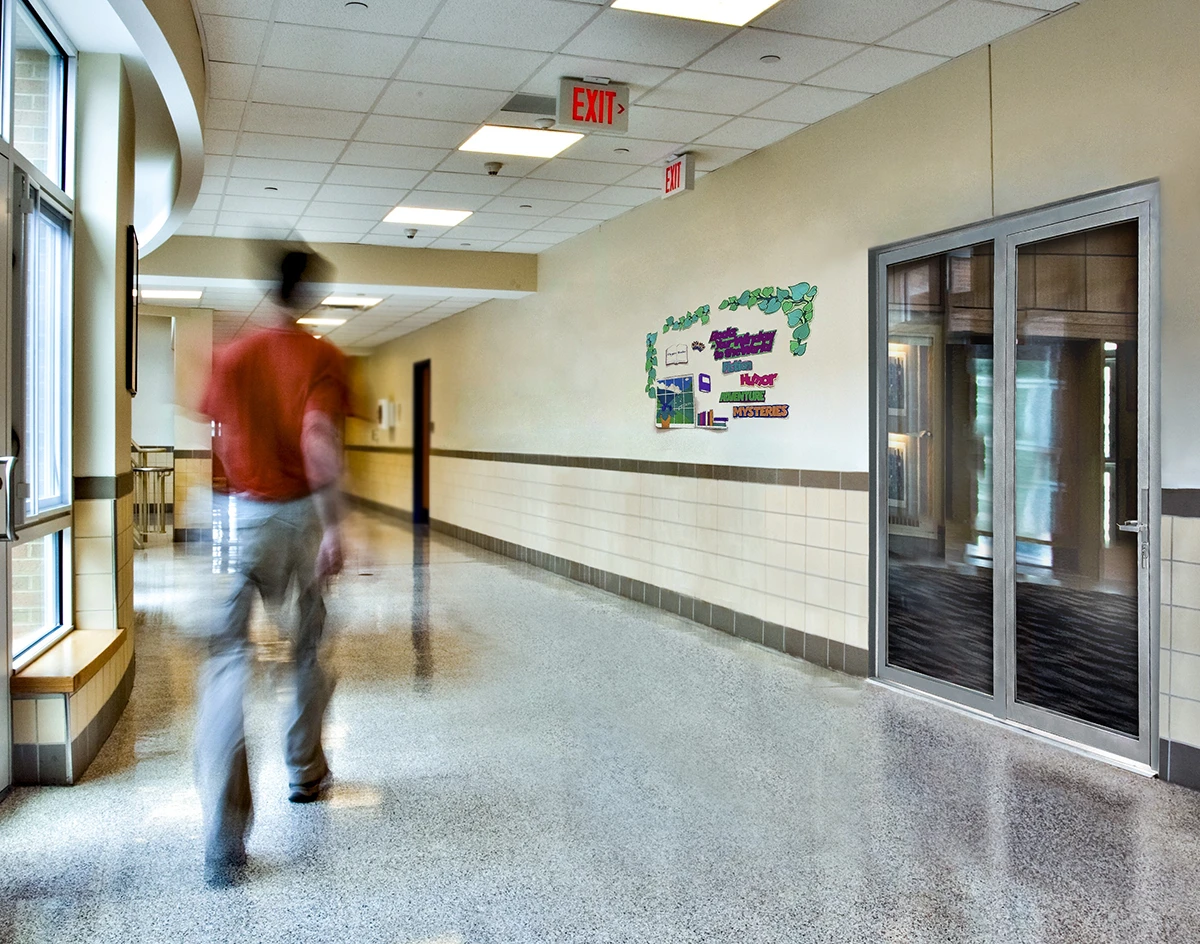
Product Innovation Awards - TGProtect
Product Innovation Awards - TGProtect
Date: Dec 2024
Publication: BUILDINGS
>>
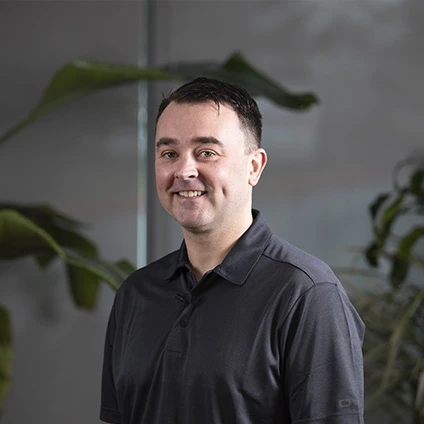
A Finger on the Pulse
A Finger on the Pulse
Date: Dec 2024
Publication: US Glass
>>
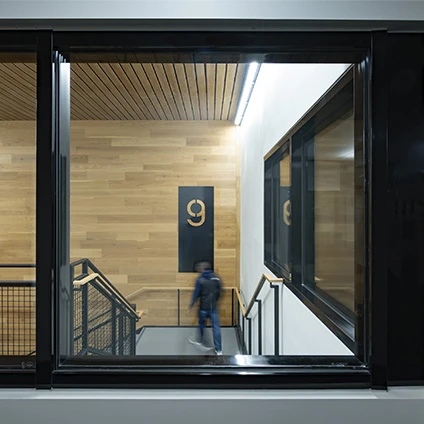
Seeing through with Safety
Seeing through with Safety
Date: Nov 2024
Publication: Architectural West
>>
A Transparent Look at Safer School Design
A Transparent Look at Safer School Design
Date: Sept 2024
Publication: Seattle Daily Journal of Commerce
>>
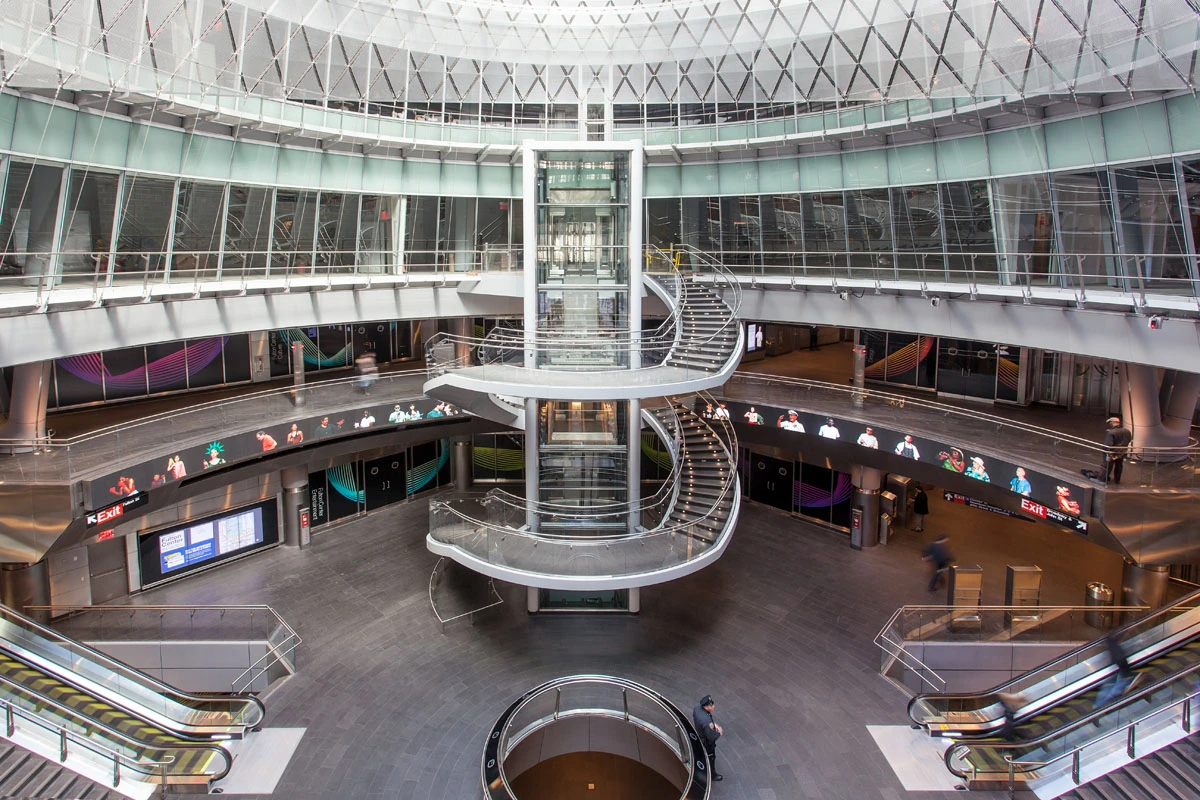
The Mettle of Metal
The Mettle of Metal
Date: Aug 2024
Publication: Metal Architecture
>>
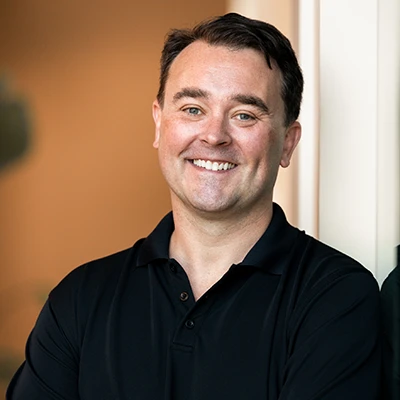
US Glass Most Influential People
US Glass Most Influential People
Date: Aug 2024
Publication: US Glass
>>
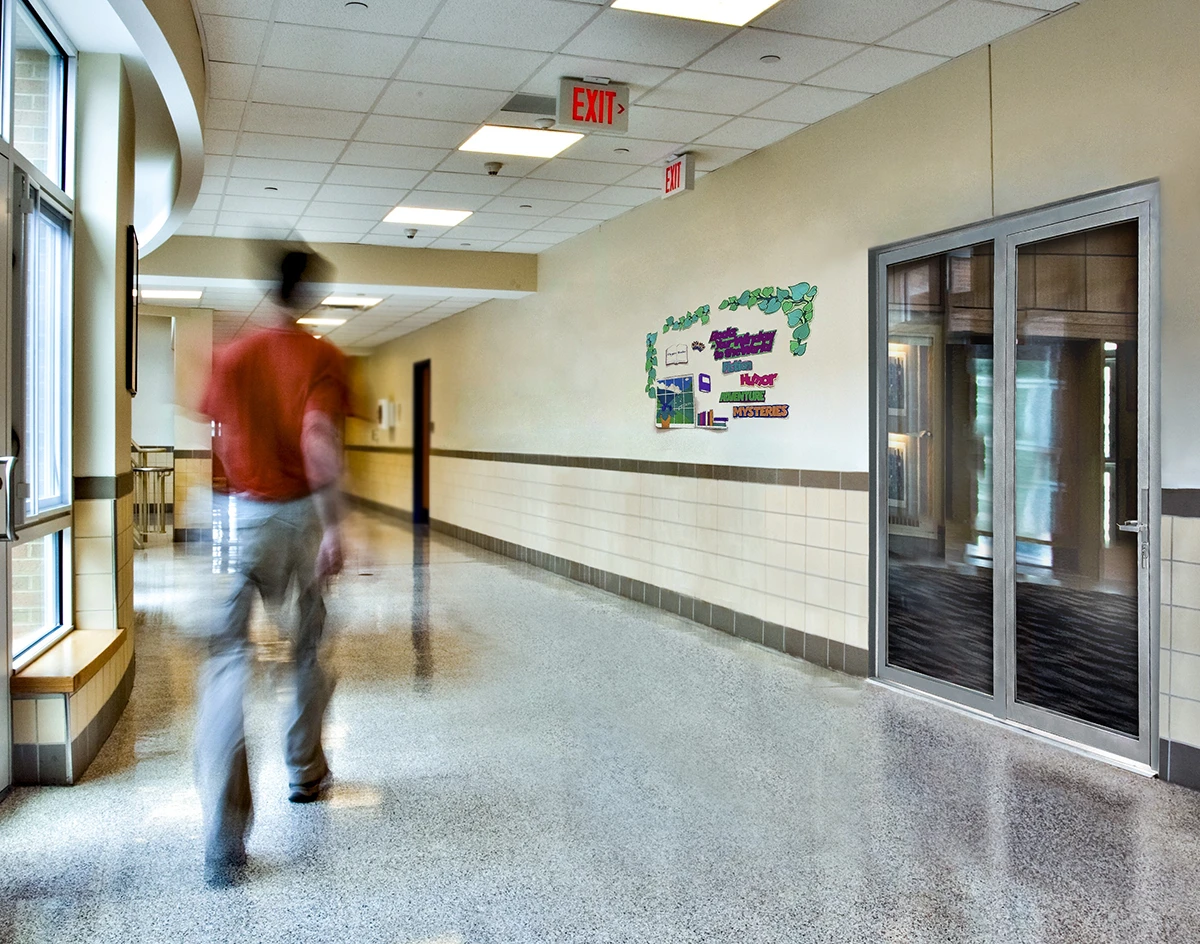
spaces4learning Product of the Year
spaces4learning Product of the Year
Date: Aug 2024
Publication: spaces4learning
>>
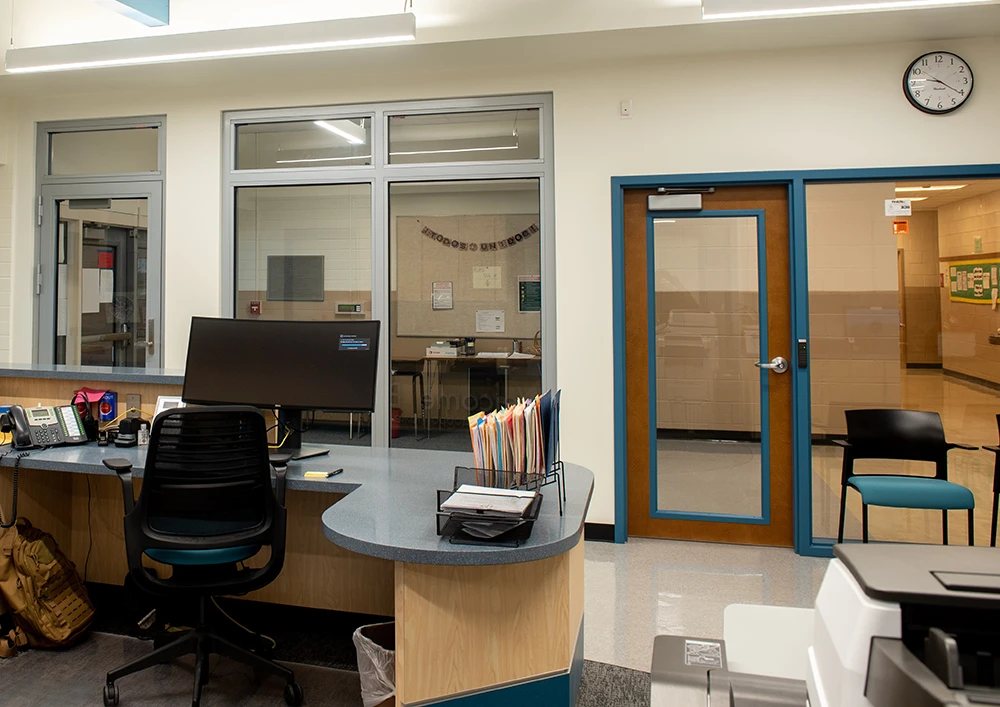
Enhanced School Security Solutions
Enhanced School Security Solutions
Date: July 2024
Publication: Glass Magazine
>>
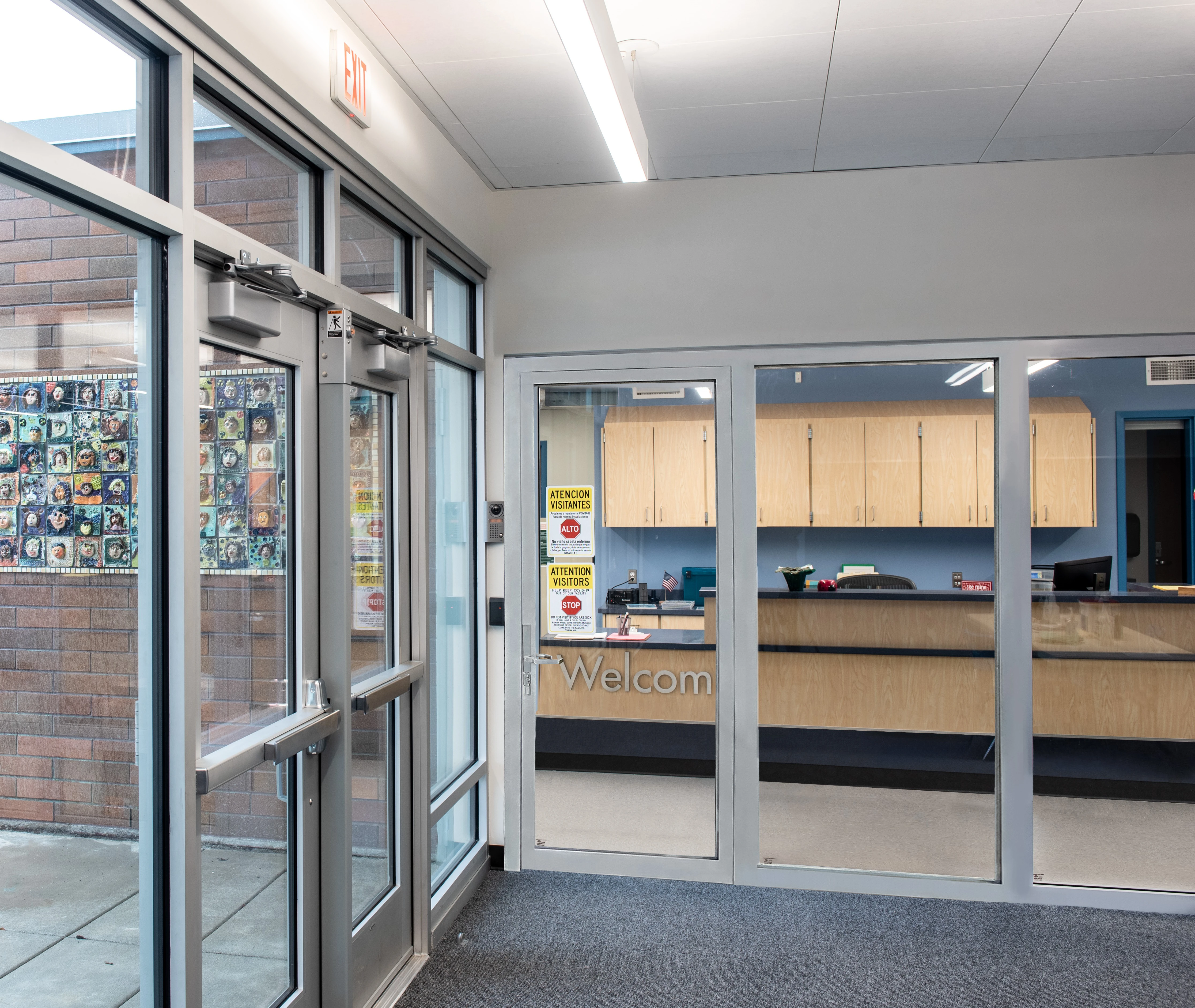
Blazing Trends: The Surging Demand For Fire-Rated Glass
Blazing Trends: The Surging Demand For Fire-Rated Glass
Date: July 2024
Publication: Glass Magazine
>>
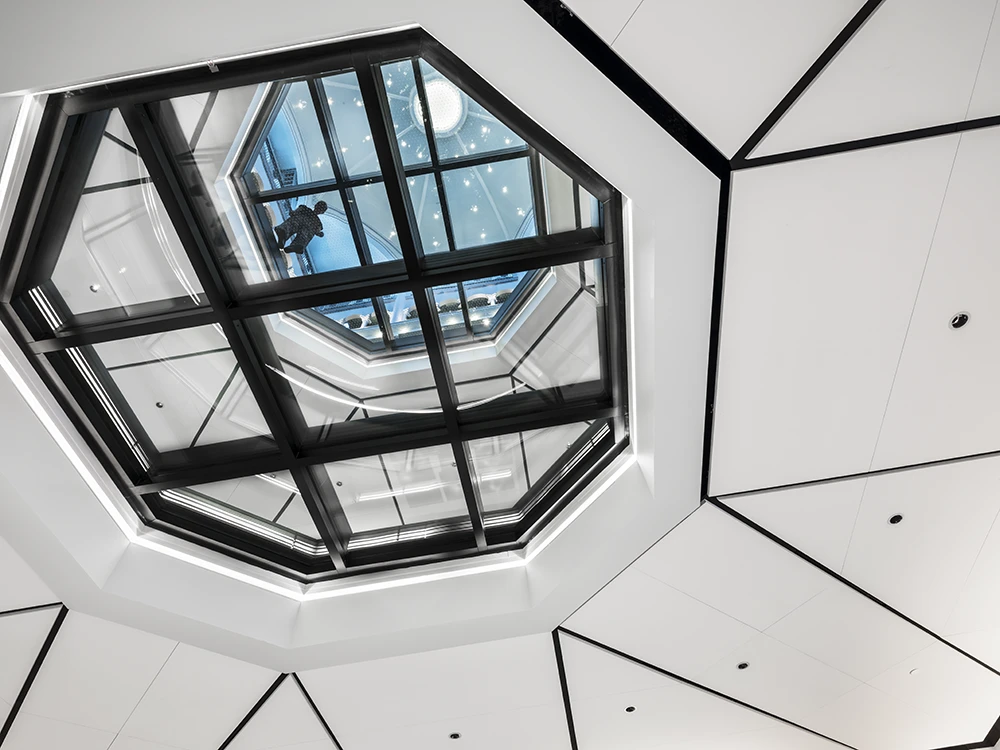
Spotlight on Fire-Rated Glazing Installations
Spotlight on Fire-Rated Glazing Installations
Date: June 2024
Publication: US Glass
>>
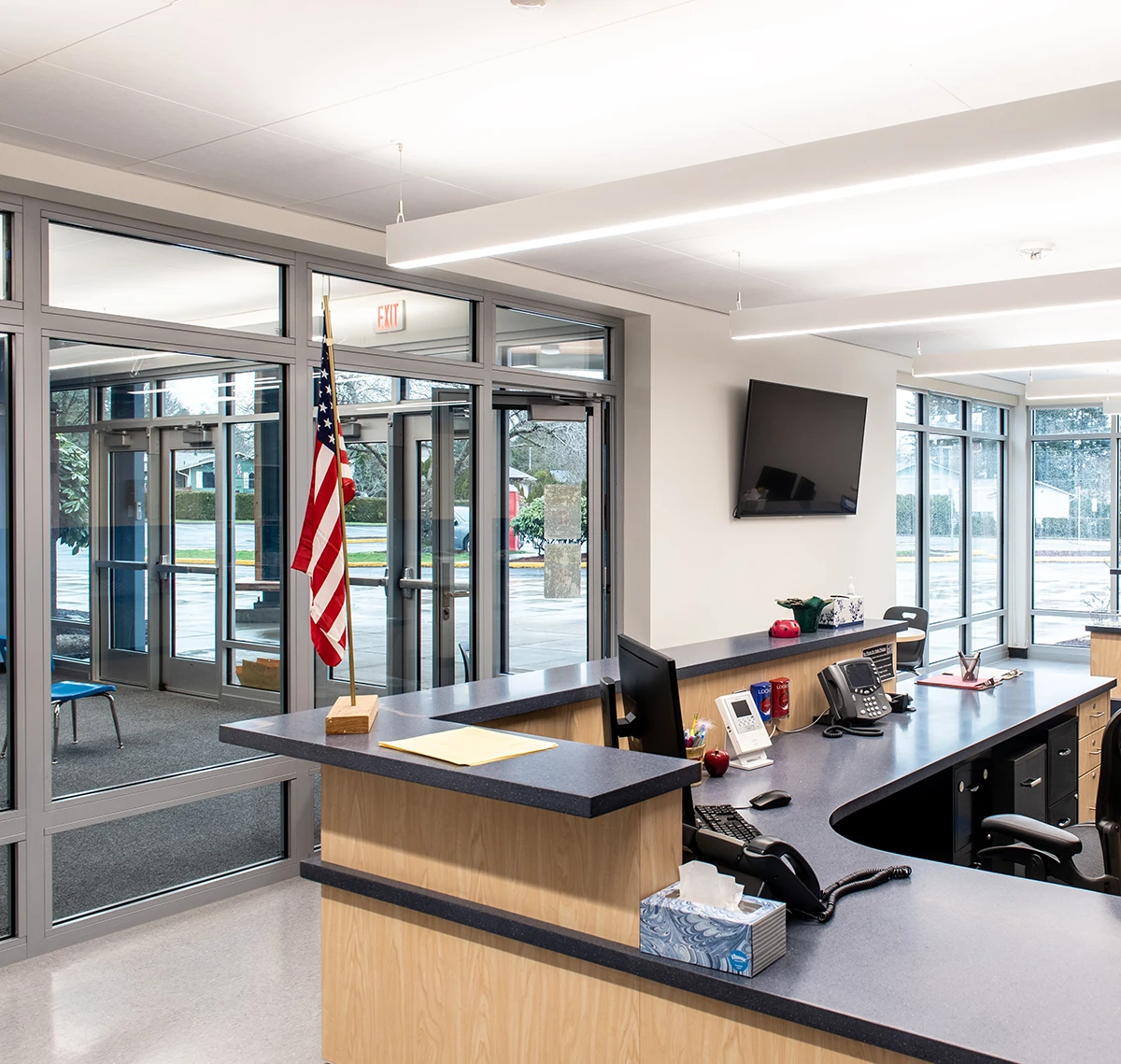
Navigating Safer School Design
Navigating Safer School Design
Date: May 2024
Publication: Door Security + Safety
>>
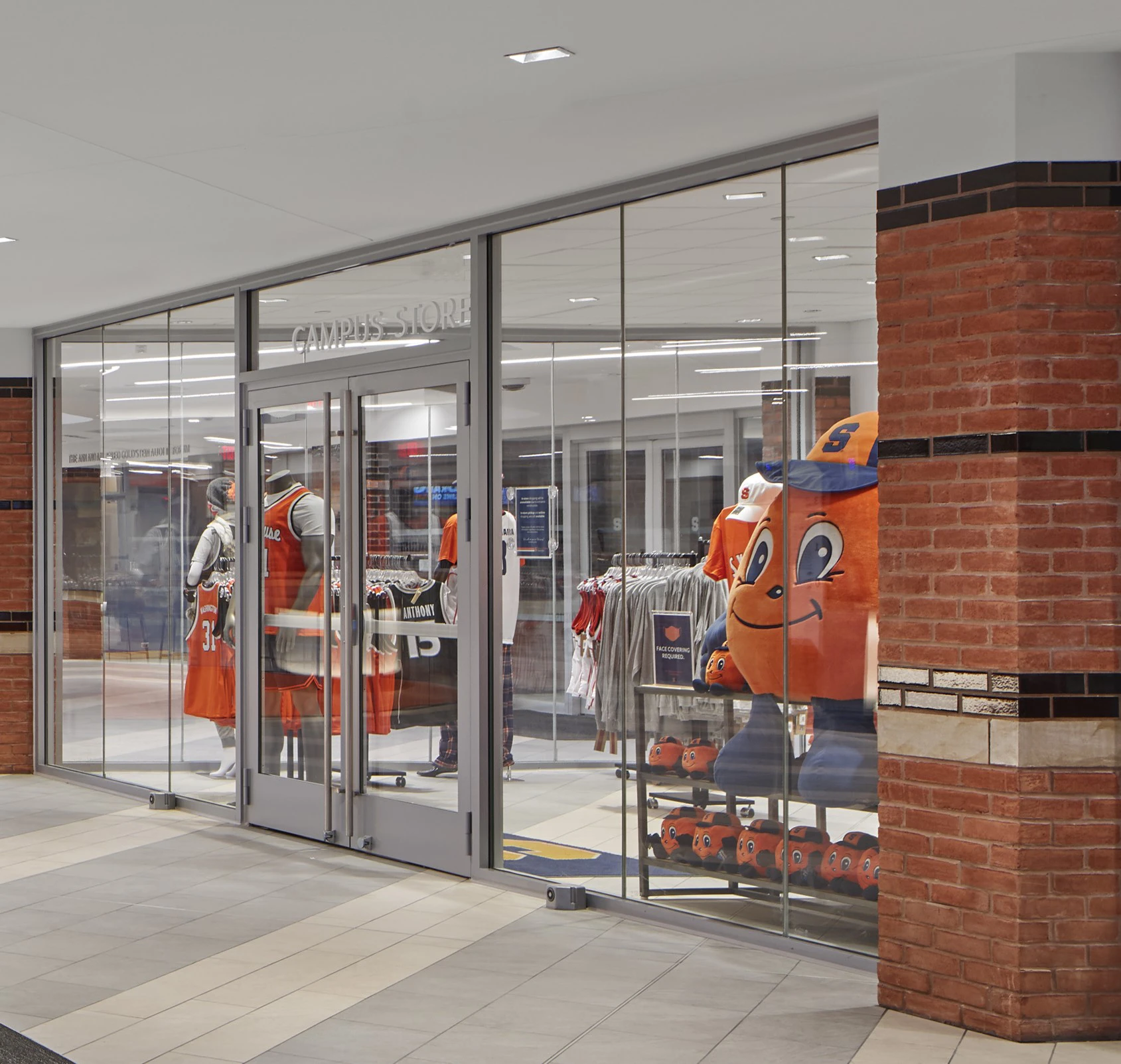
An Answer 35 years in the Making
An Answer 35 years in the Making
Date: Apr 2024
Publication: Life Safety Digest
>>
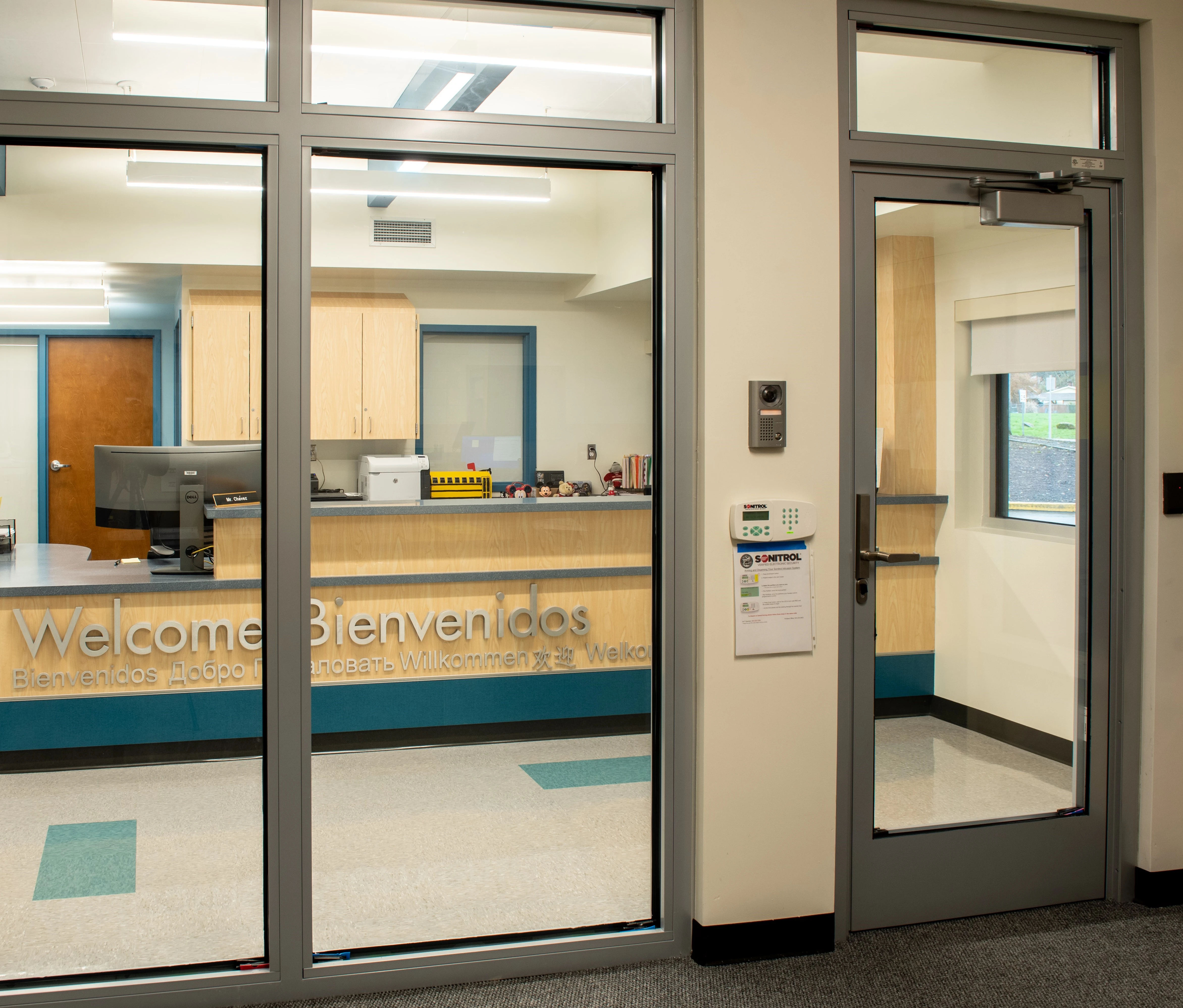
Opening the Conversation to Code-Compliant School Security
Opening the Conversation to Code-Compliant School Security
Date: Mar 2024
Publication: Security Management
>>
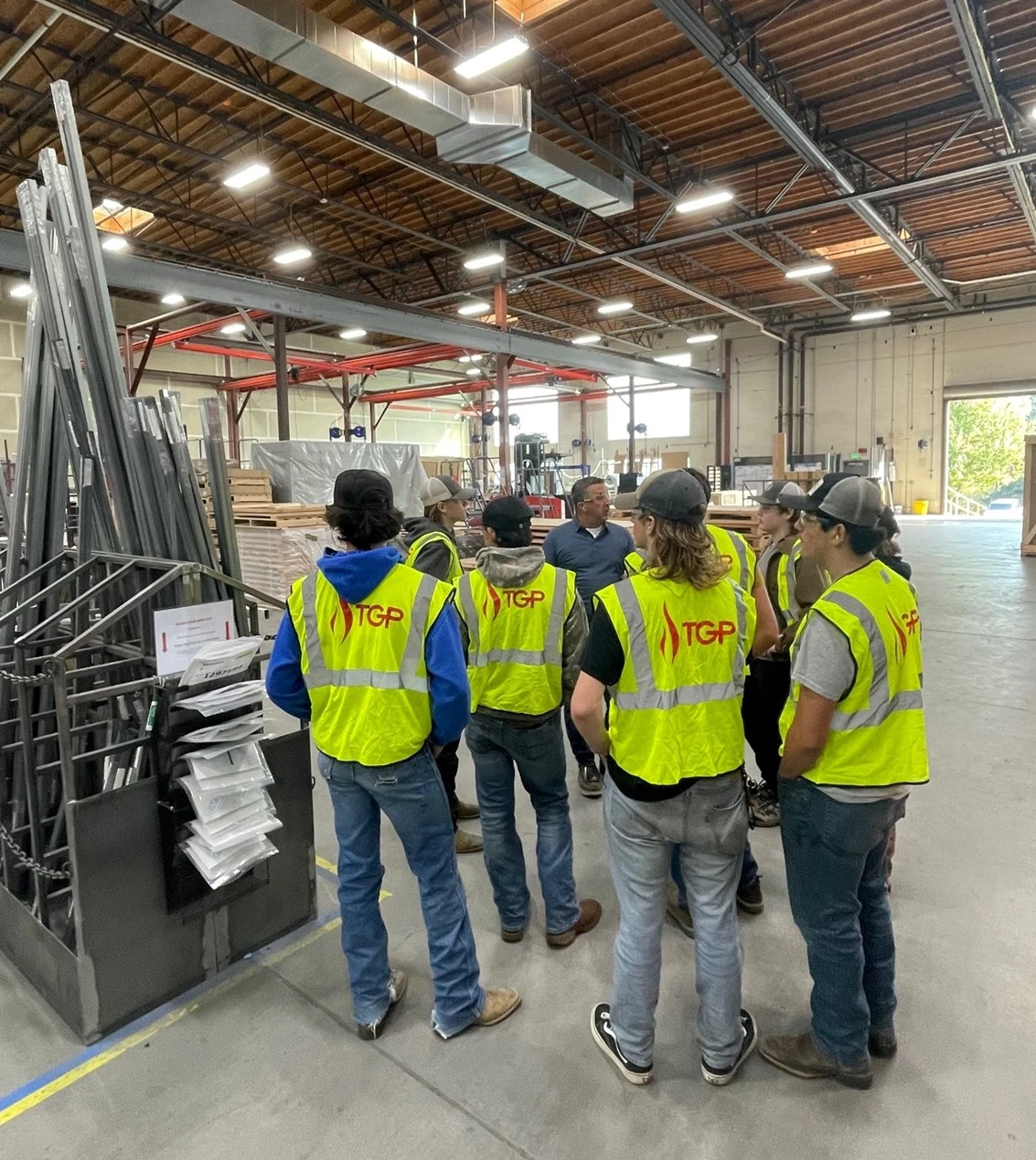
Recruiting Young Talent in the Glass Industry
Recruiting Young Talent in the Glass Industry
Date: Feb 2024
Publication: Glass Magazine
>>
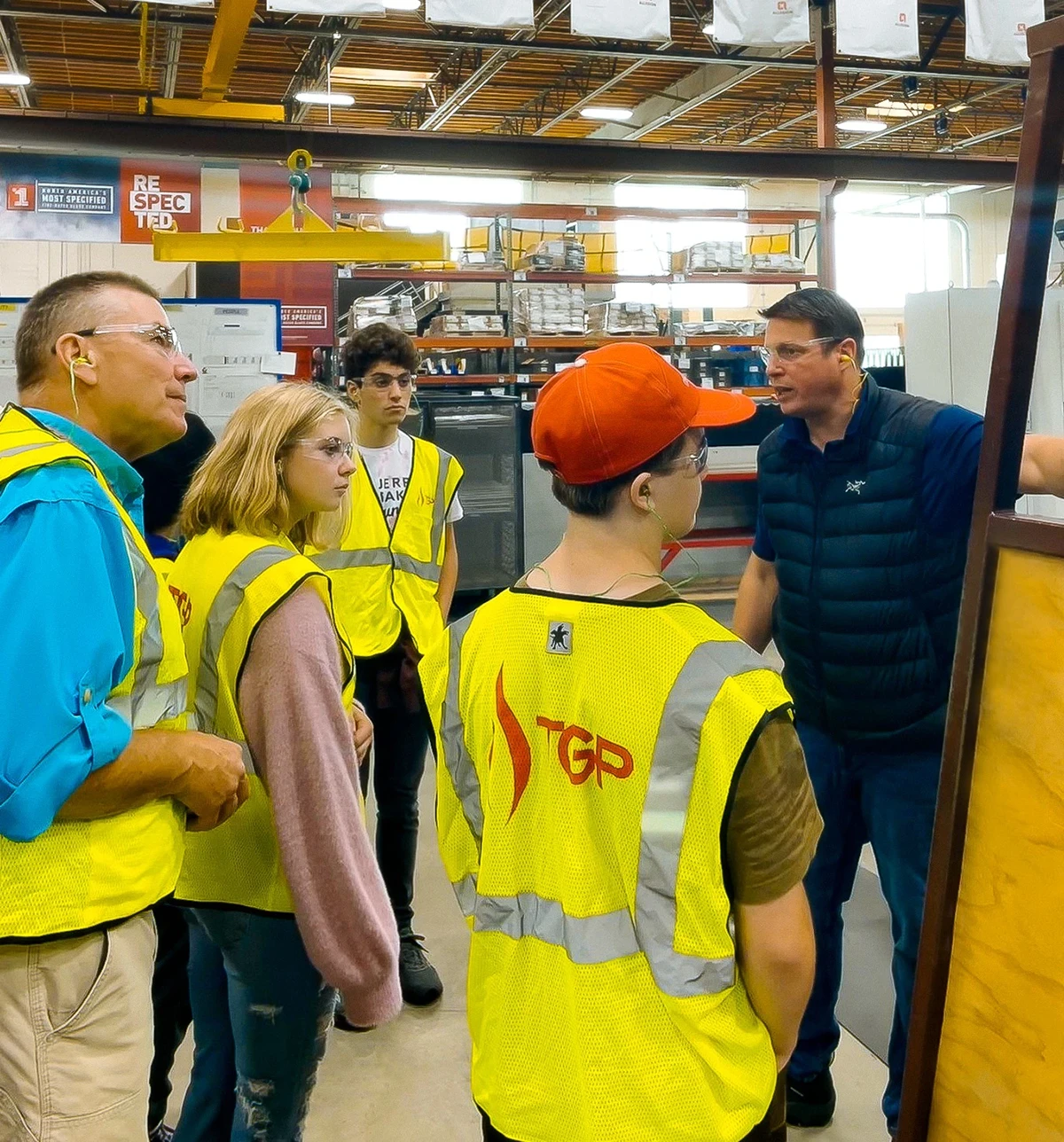
Allegion's Technical Glass Products Hosts Students for MFG Day
Allegion's Technical Glass Products Hosts Students for MFG Day
Date: Feb 2024
Publication: Door Security + Safety
>>
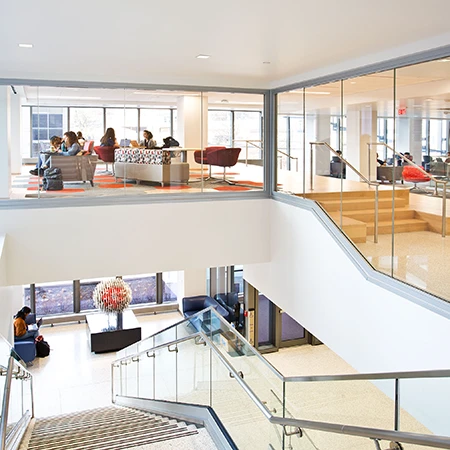
Balancing Act
Balancing Act
Date: Jan 2024
Publication: USGlass Magazine
>>
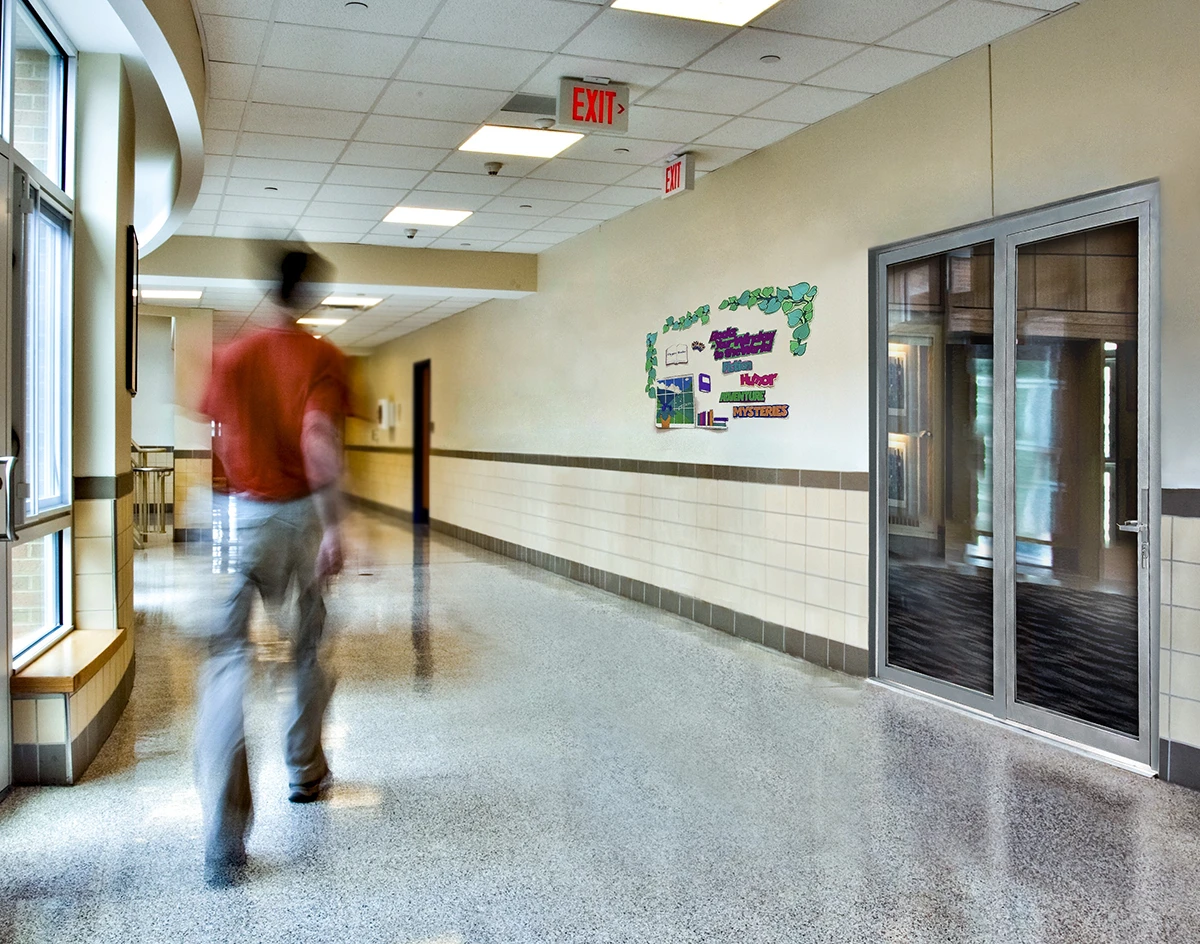
Fire protection devices offer complex solutions
Fire protection devices offer complex solutions
Date: Dec 2023
Publication: Healthcare Facilities Management
>>
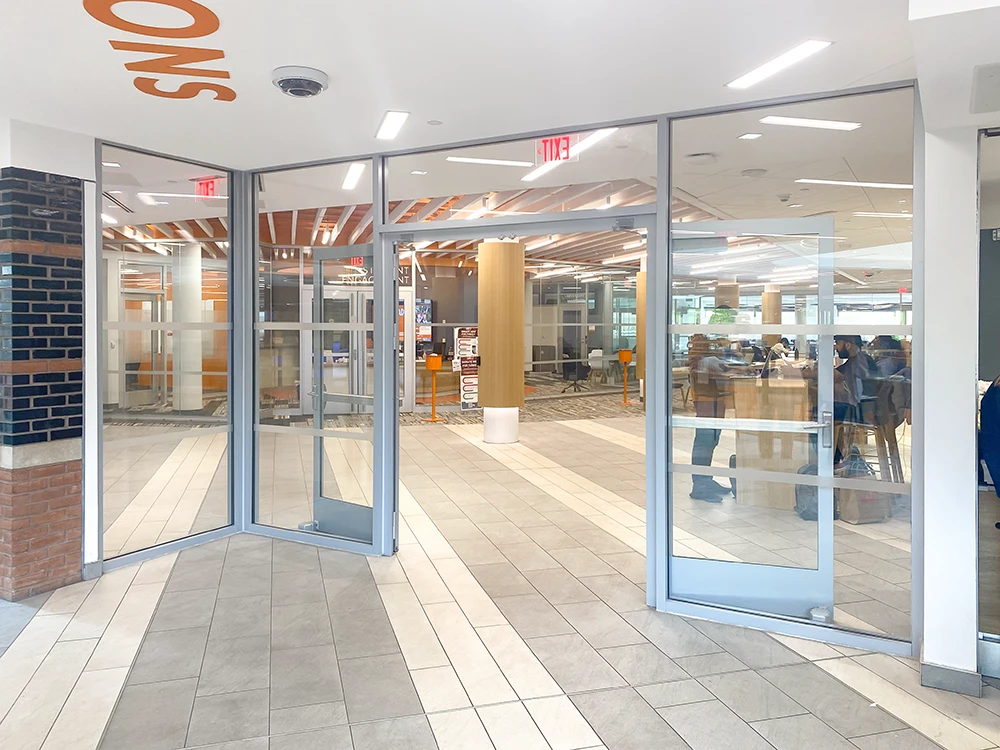
A Dramatic Shift
A Dramatic Shift
Date: Nov 2023
Publication: Door Security + Safety
>>
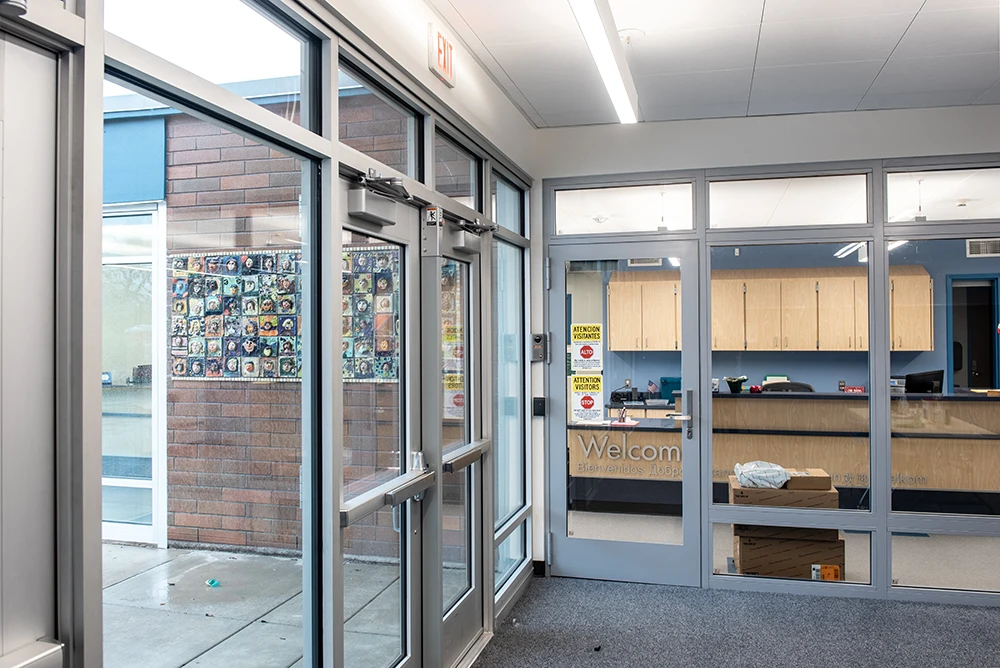
Designing Entry Vestibules for Schools
Designing Entry Vestibules for Schools
Date: Nov 2023
Publication: Door Security + Safety
>>
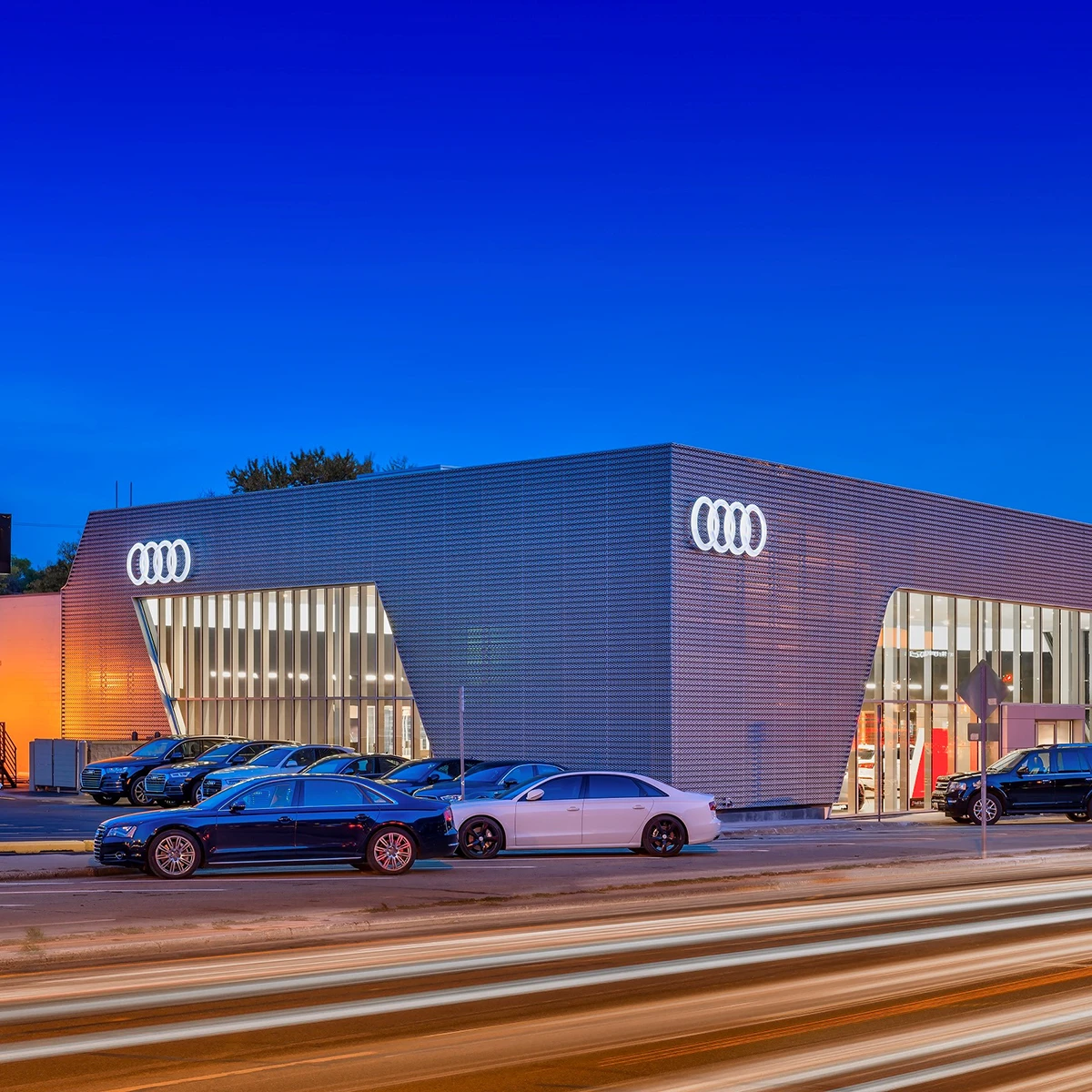
Exterior Fire-Rated Glazing Code Compliance without Compromise
Exterior Fire-Rated Glazing Code Compliance without Compromise
Date: Aug 2023
Publication: Building Enclosure
>>
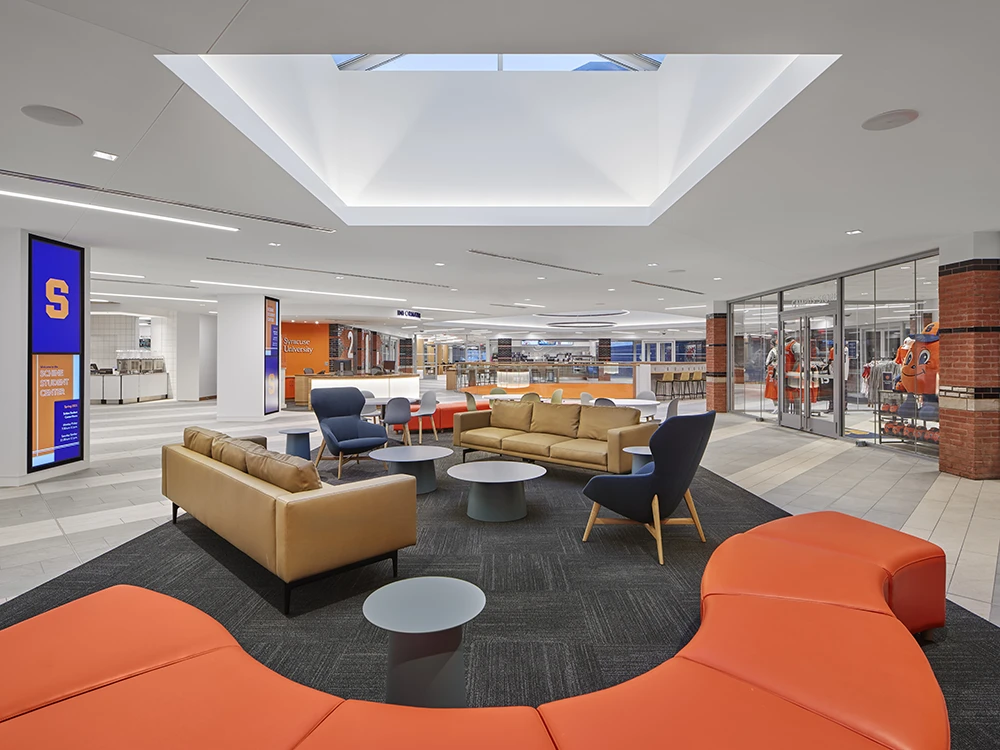
Architects Redesign Syracuse University Student Center
Architects Redesign Syracuse University Student Center
Date: Oct 2023
Publication: Glass Magazine
>>
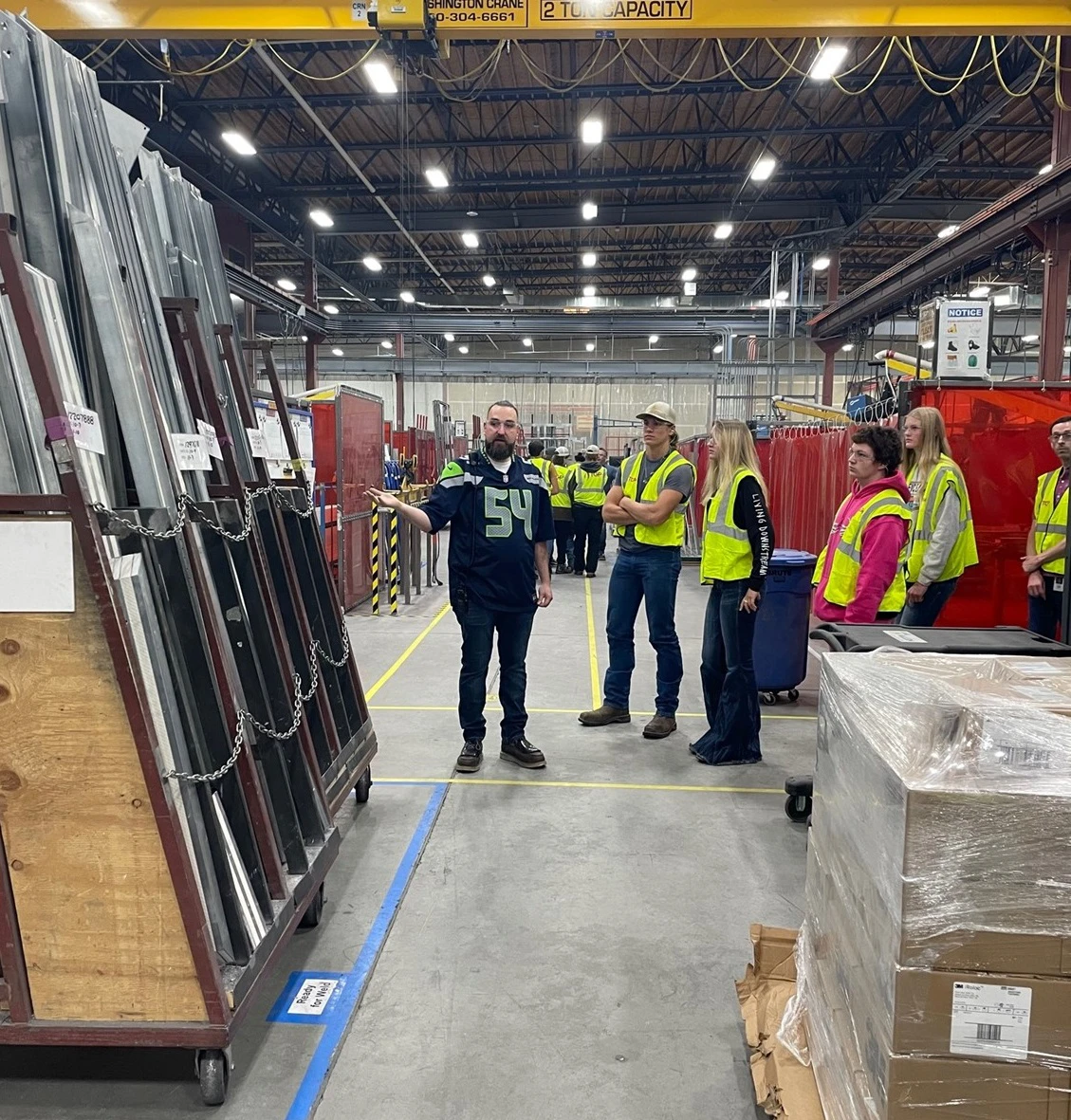
TGP Seeks to Bridge Skills Gap with 2023 Manufacturing Day Event
TGP Seeks to Bridge Skills Gap with 2023 Manufacturing Day Event
Date: Oct 2023
Publication: US Glass
>>
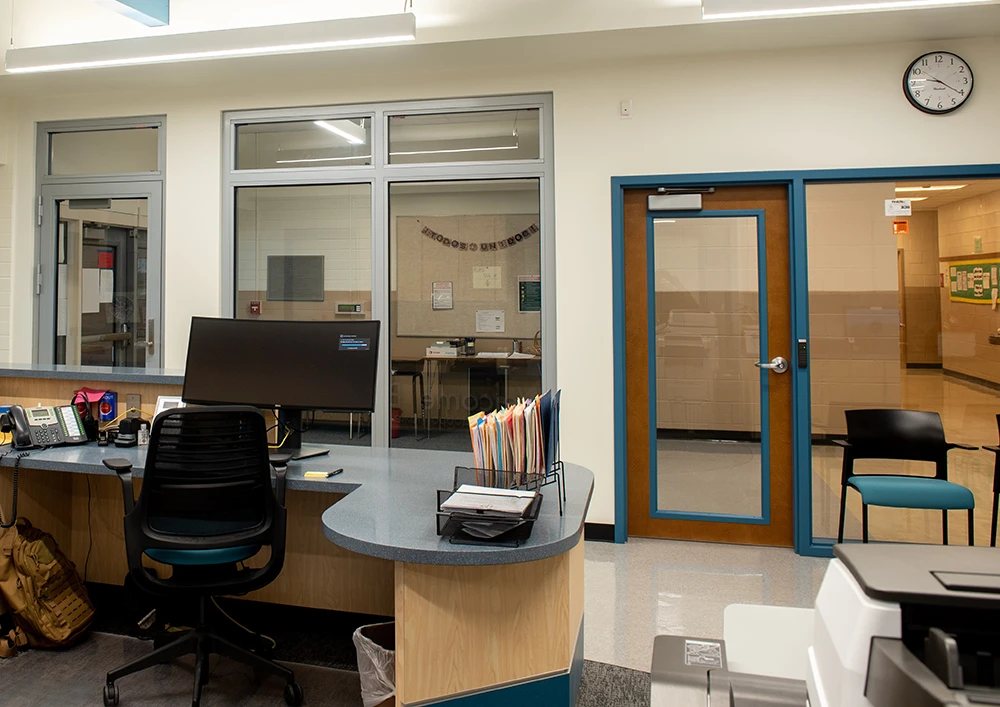
Secured School Entry Vestibules: Reducing Weak Points and Increasing Sightlines
Secured School Entry Vestibules: Reducing Weak Points and Increasing Sightlines
Date: Sept 2023
Publication: Campus Safety
>>
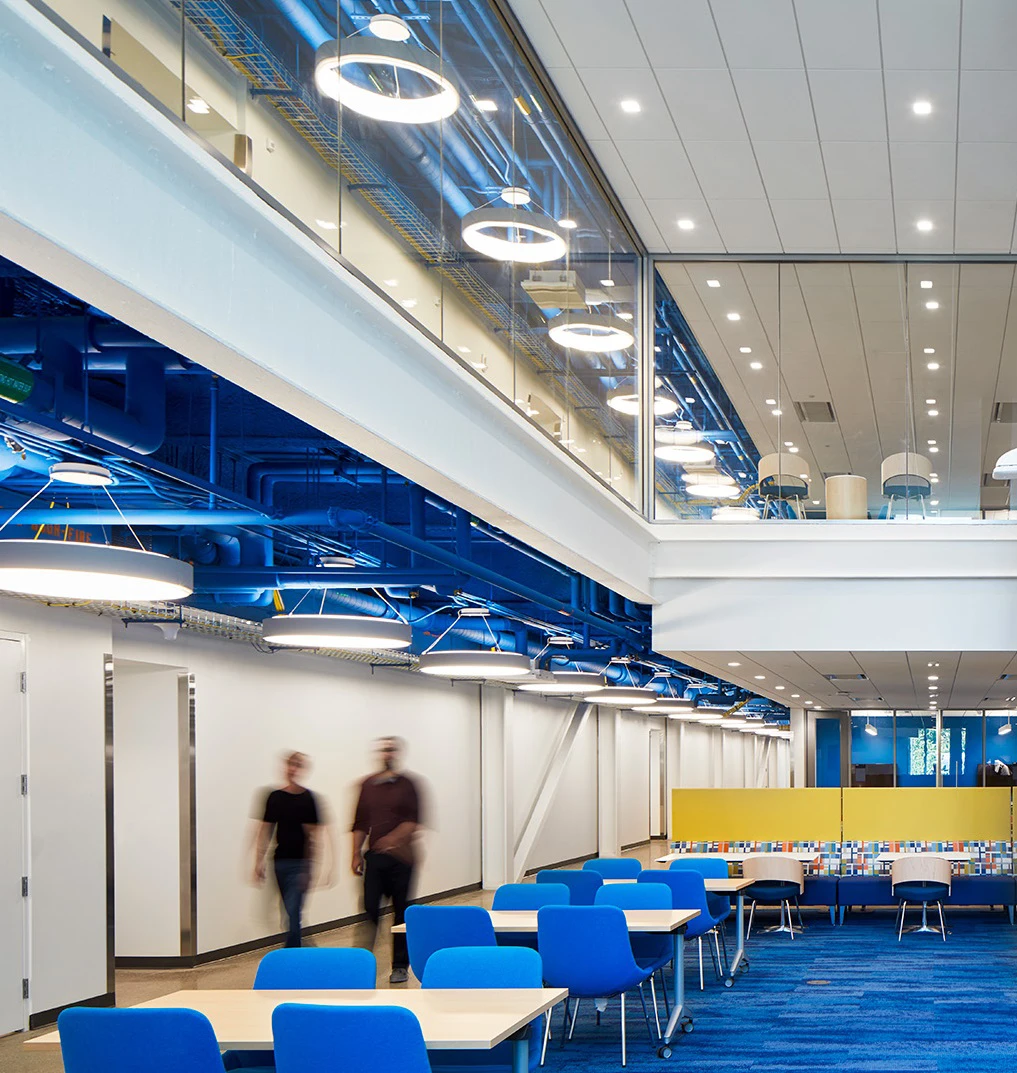
William R. Murchie Science Building
William R. Murchie Science Building
Date: Sept 2023
Publication: Retrofit
>>
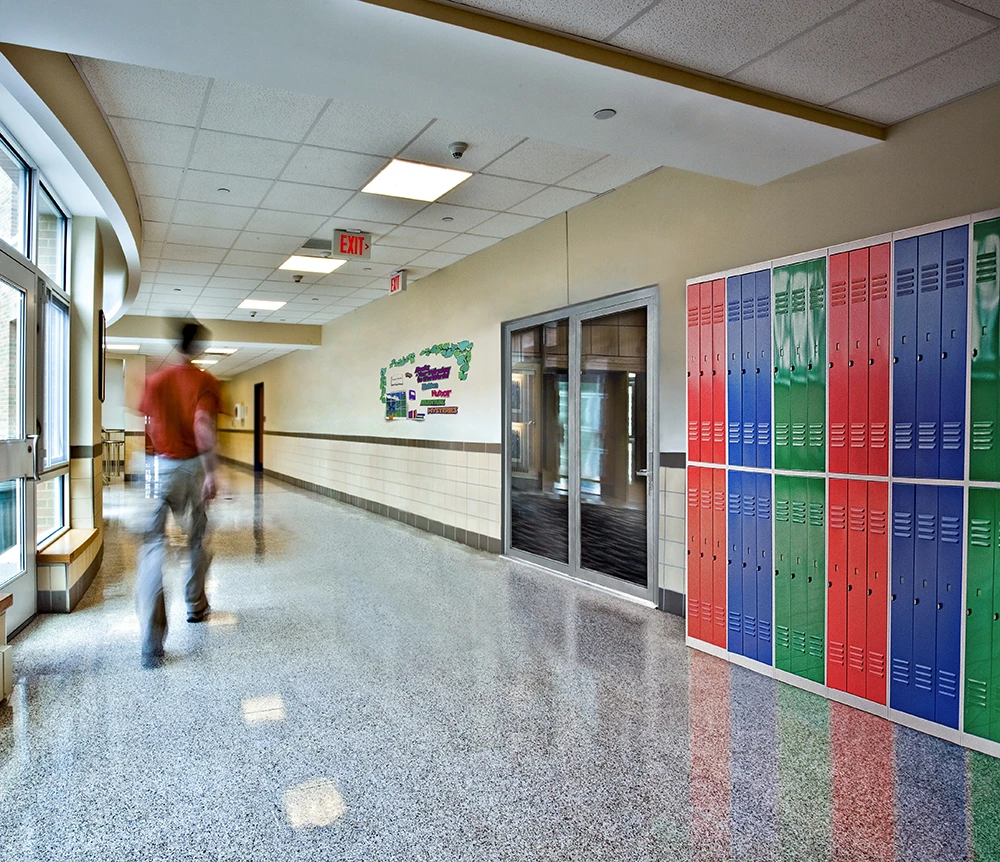
Invisible Protection: Hardening Entrances with Multifunctional, Fire-Rated Glass
Invisible Protection: Hardening Entrances with Multifunctional, Fire-Rated Glass
Date: July 2023
Publication: Glass Magazine
>>
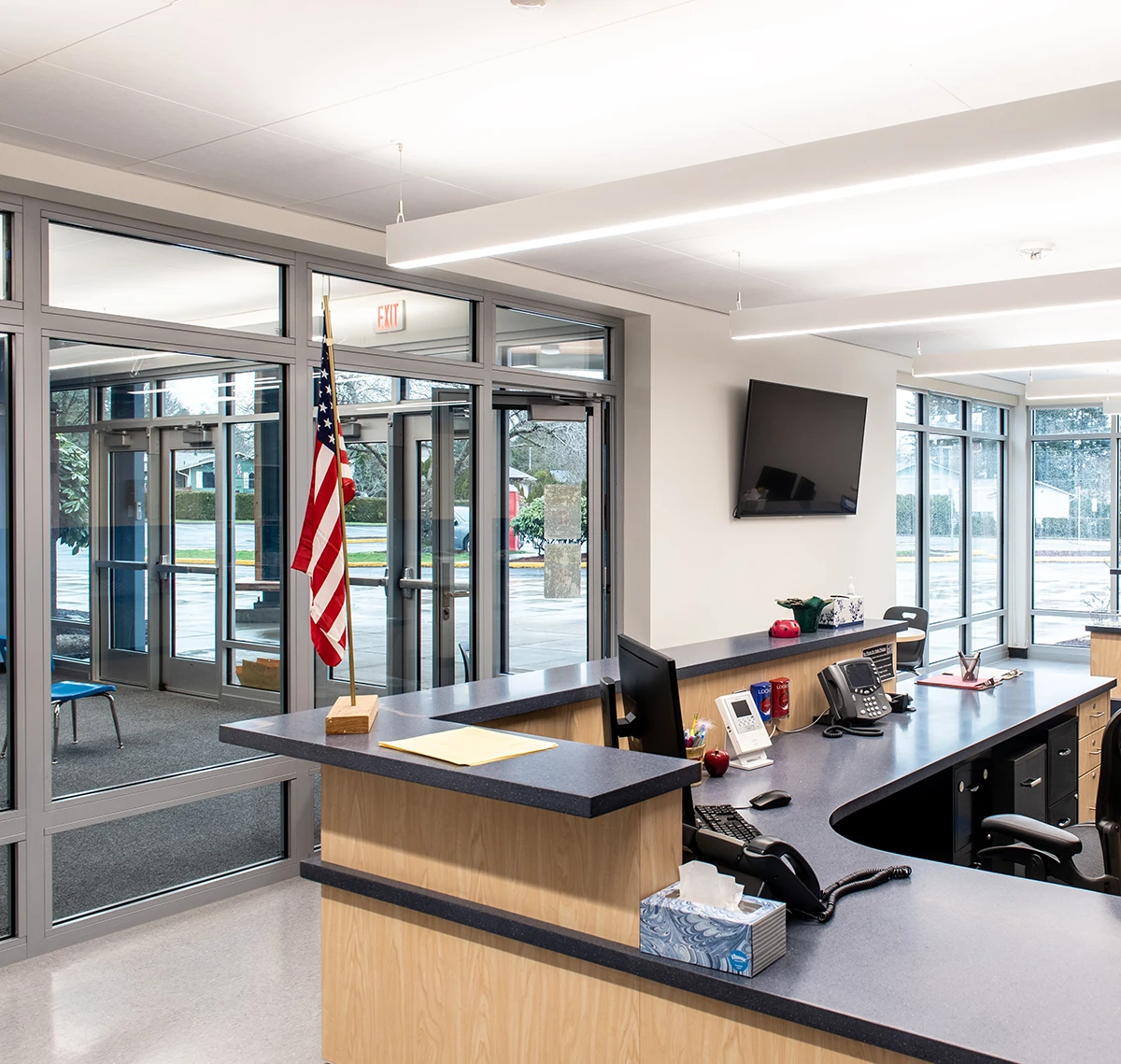
Designing Safer Schools: Considerations for Increasing School Security
Designing Safer Schools: Considerations for Increasing School Security
Date: May 2023
Publication: Campus Security and Life Safety
>>
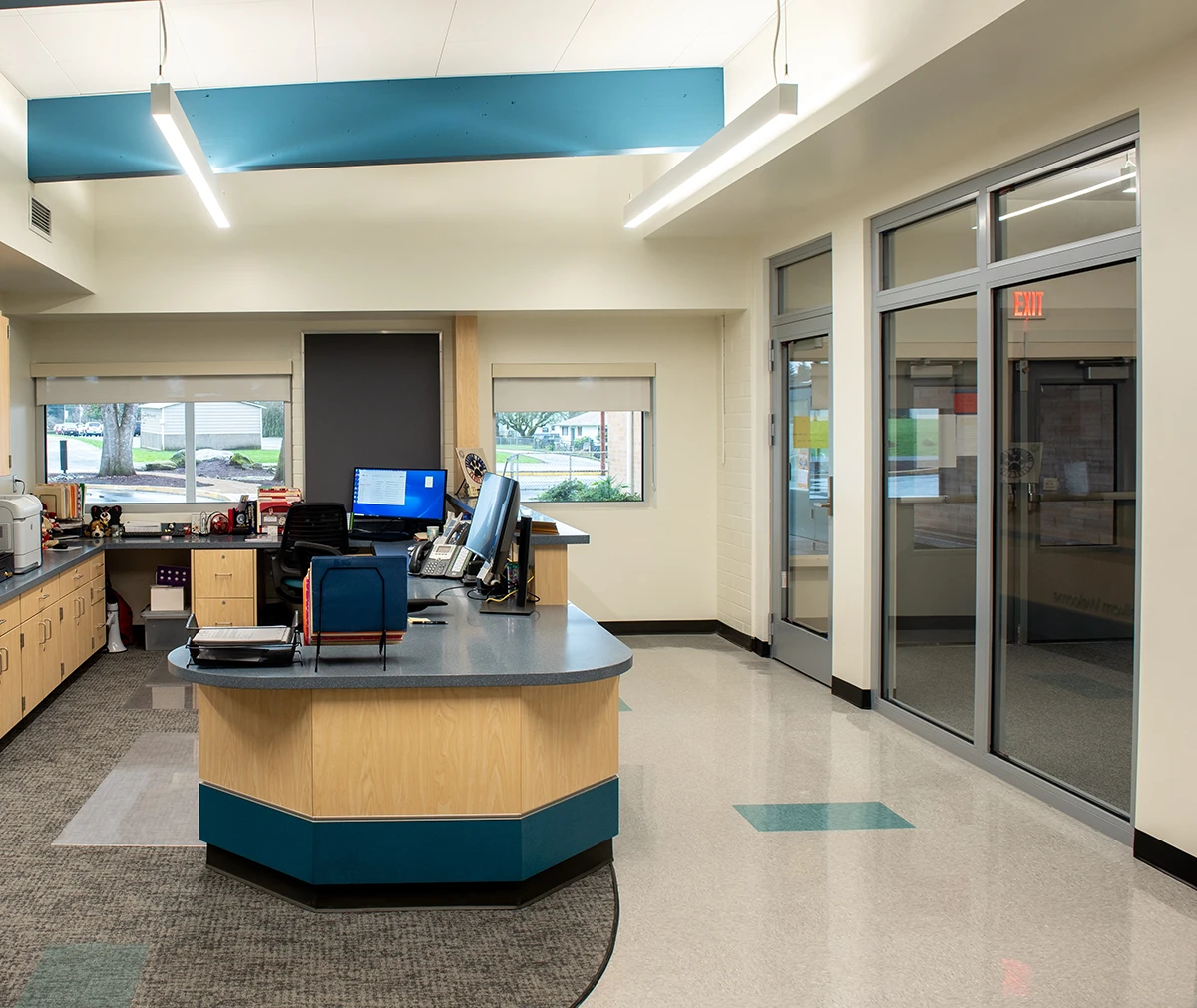
Safe Havens Within
Safe Havens Within
Date: May 2023
Publication: Door Security + Safety
>>
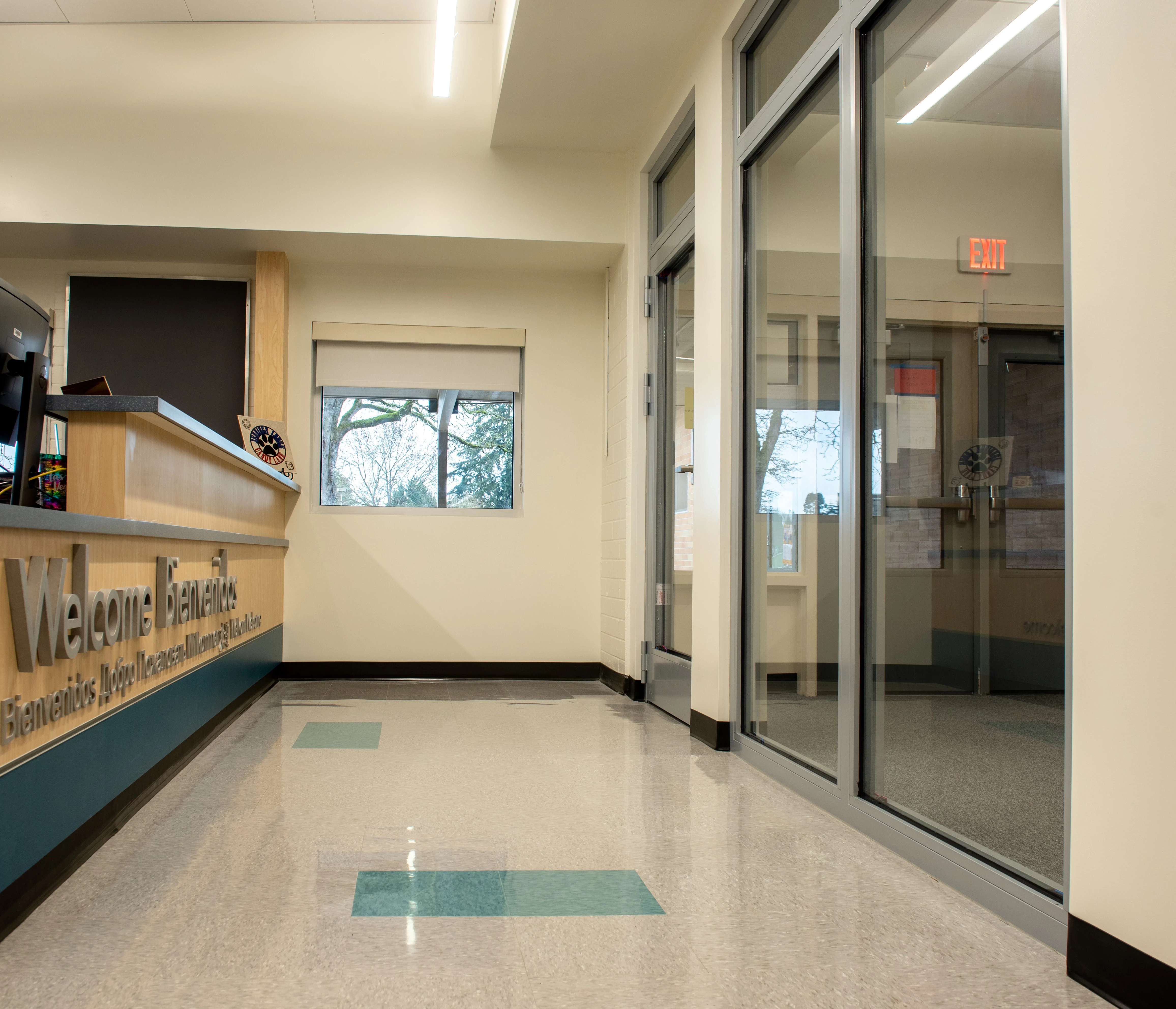
Safe and Secure at Candy Lane
Safe and Secure at Candy Lane
Date: May 2023
Publication: Door Security + Safety
>>
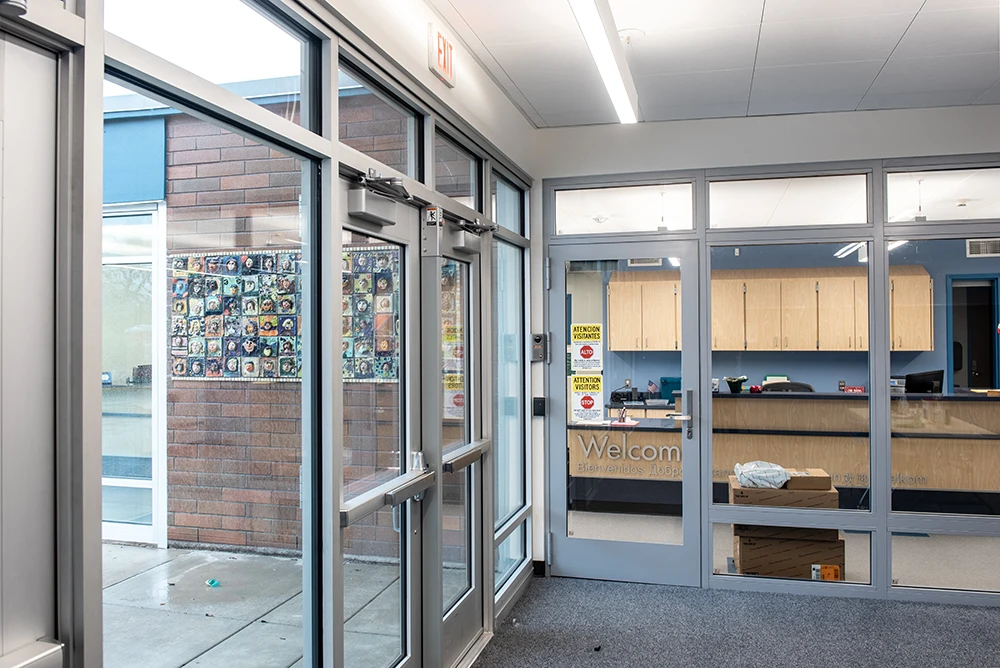
Invisible Shield
Invisible Shield
Date: Apr 2023
Publication: US Glass
>>
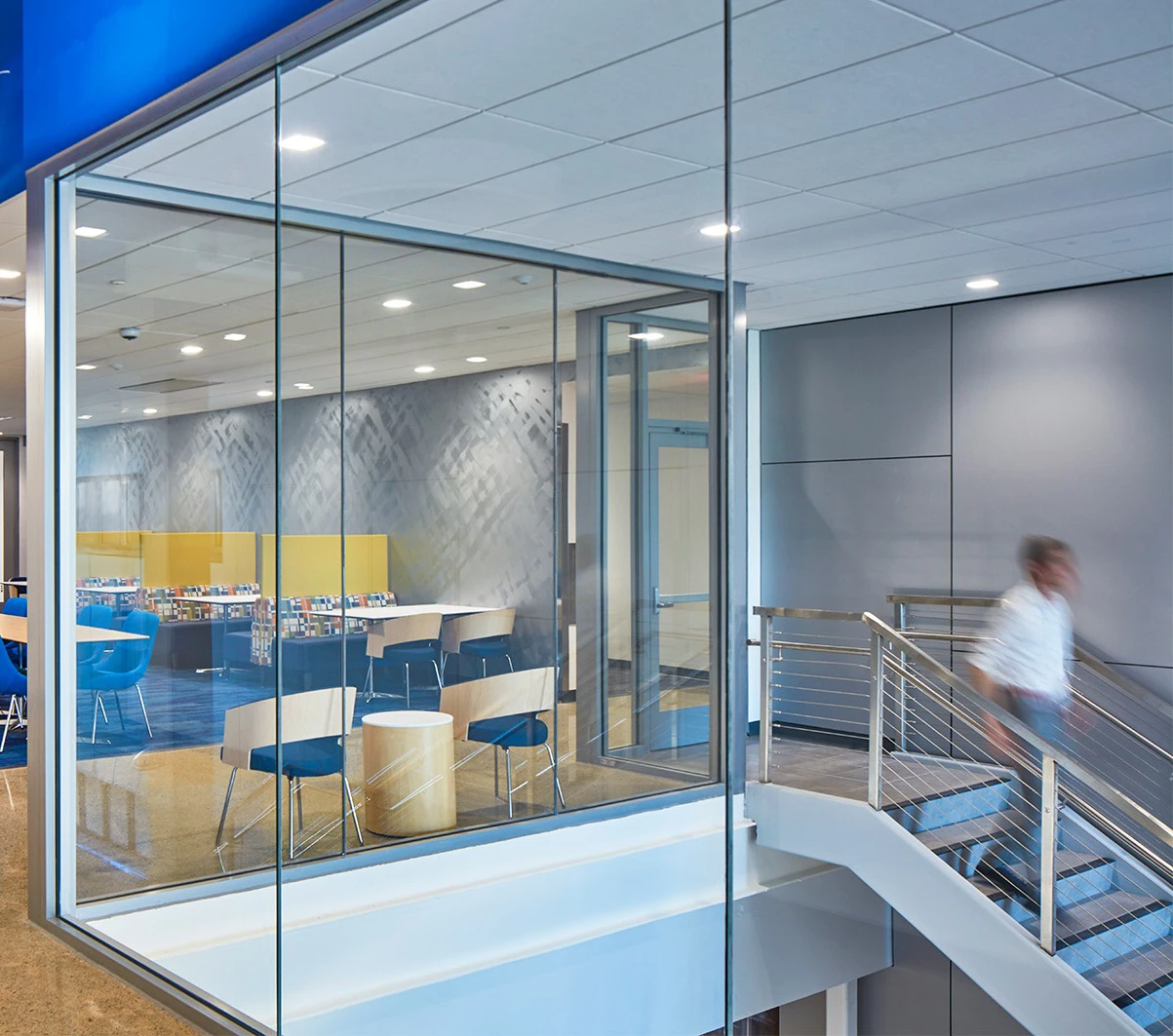
Fire-Rated Glass Satisfies Code Requirements and Design Intent in Science Building
Fire-Rated Glass Satisfies Code Requirements and Design Intent in Science Building
Date: Apr 2023
Publication: Life Safety Digest
>>
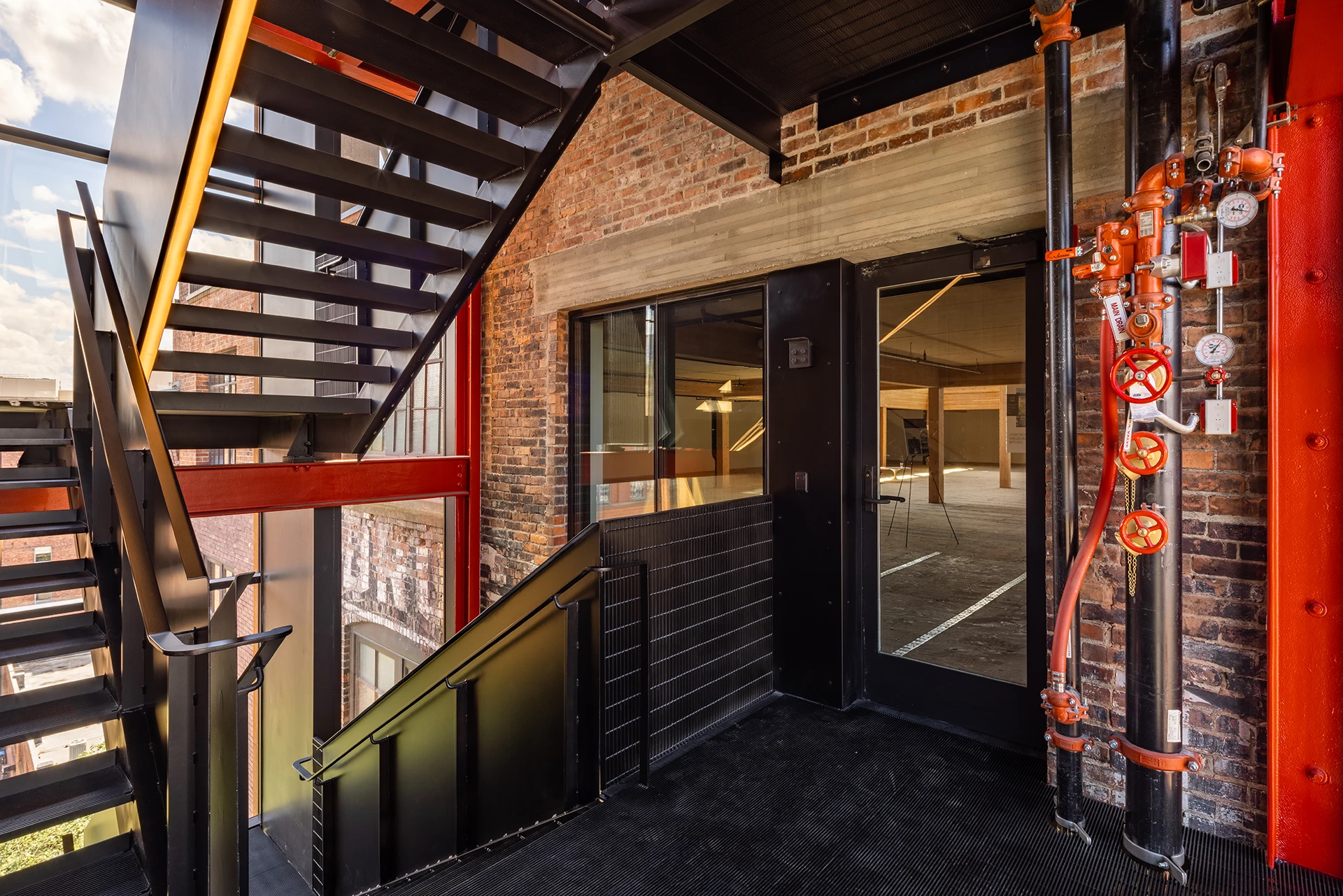
External Stairwell Meets Retrofit’s Fire-Safety and Design Requirements
External Stairwell Meets Retrofit’s Fire-Safety and Design Requirements
Date: Mar 2023
Publication: Life Safety Digest
>>
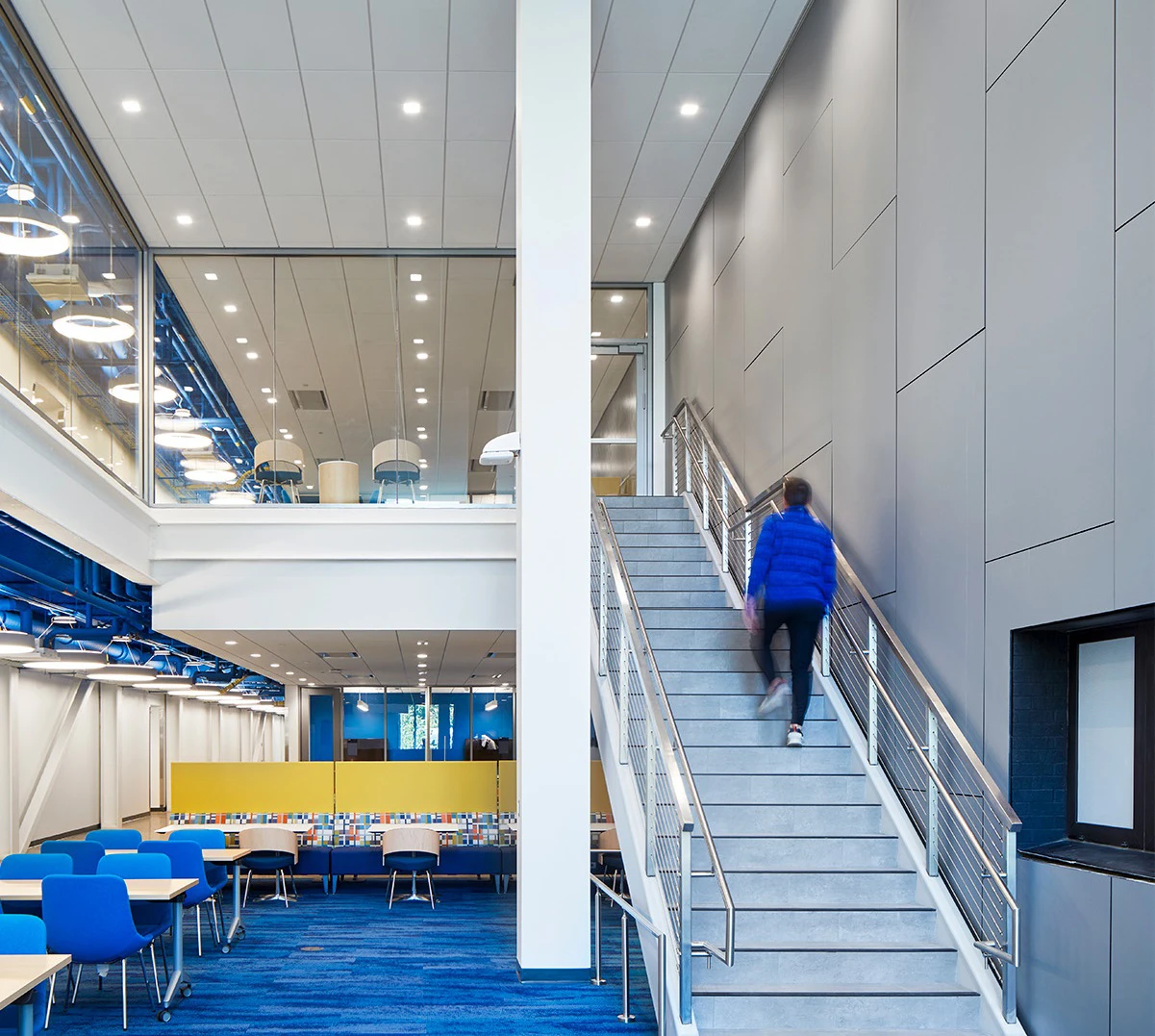
Fire-Rated Glass in Stairwell Enclosures
Fire-Rated Glass in Stairwell Enclosures
Date: Mar 2023
Publication: Walls & Ceilings
>>
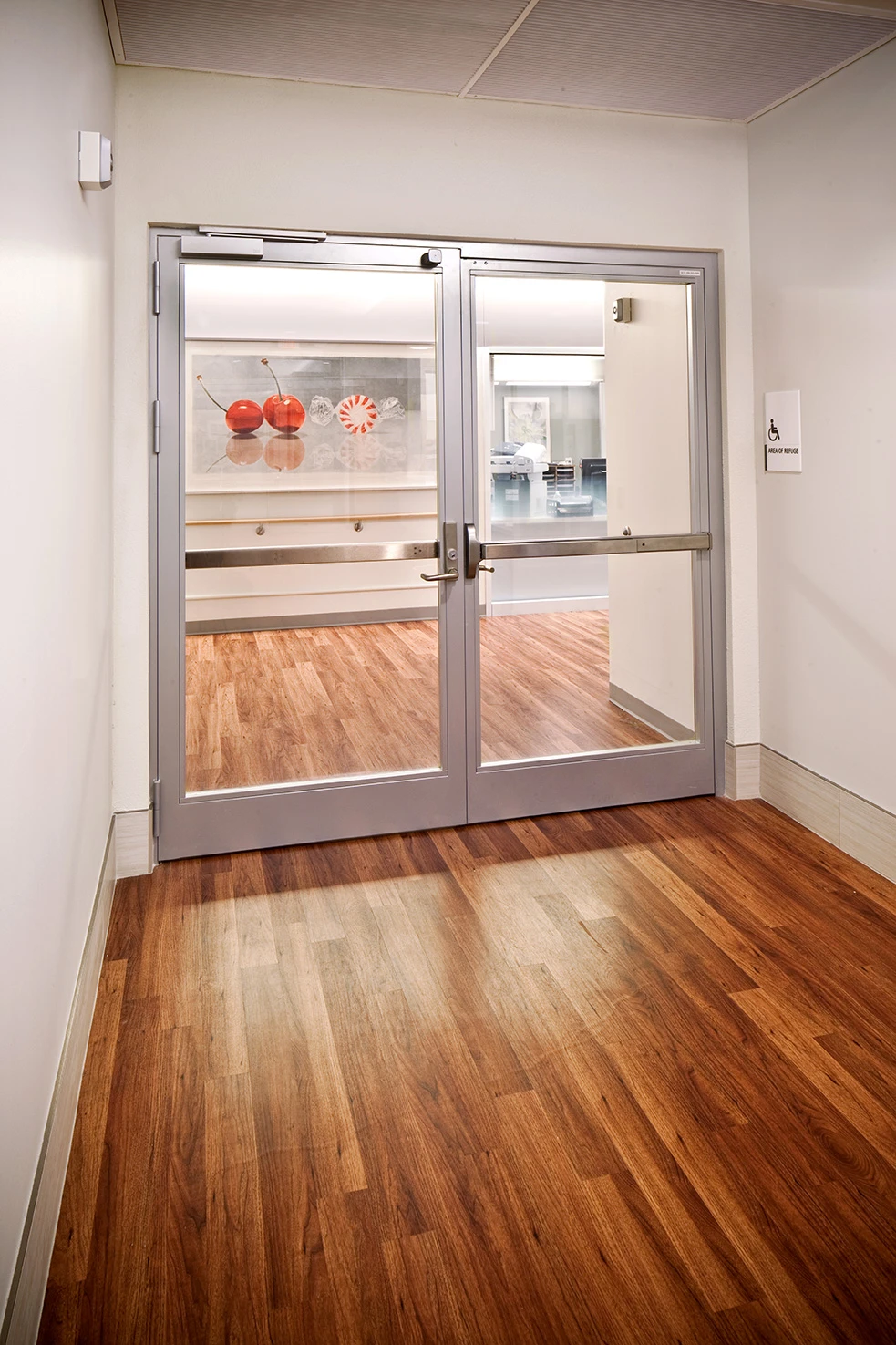
Syracuse Glass Co. to Distribute TGP Fire-Rated Glass Products
Syracuse Glass Co. to Distribute TGP Fire-Rated Glass Products
Date: Feb 2023
Publication: USGlass
>>
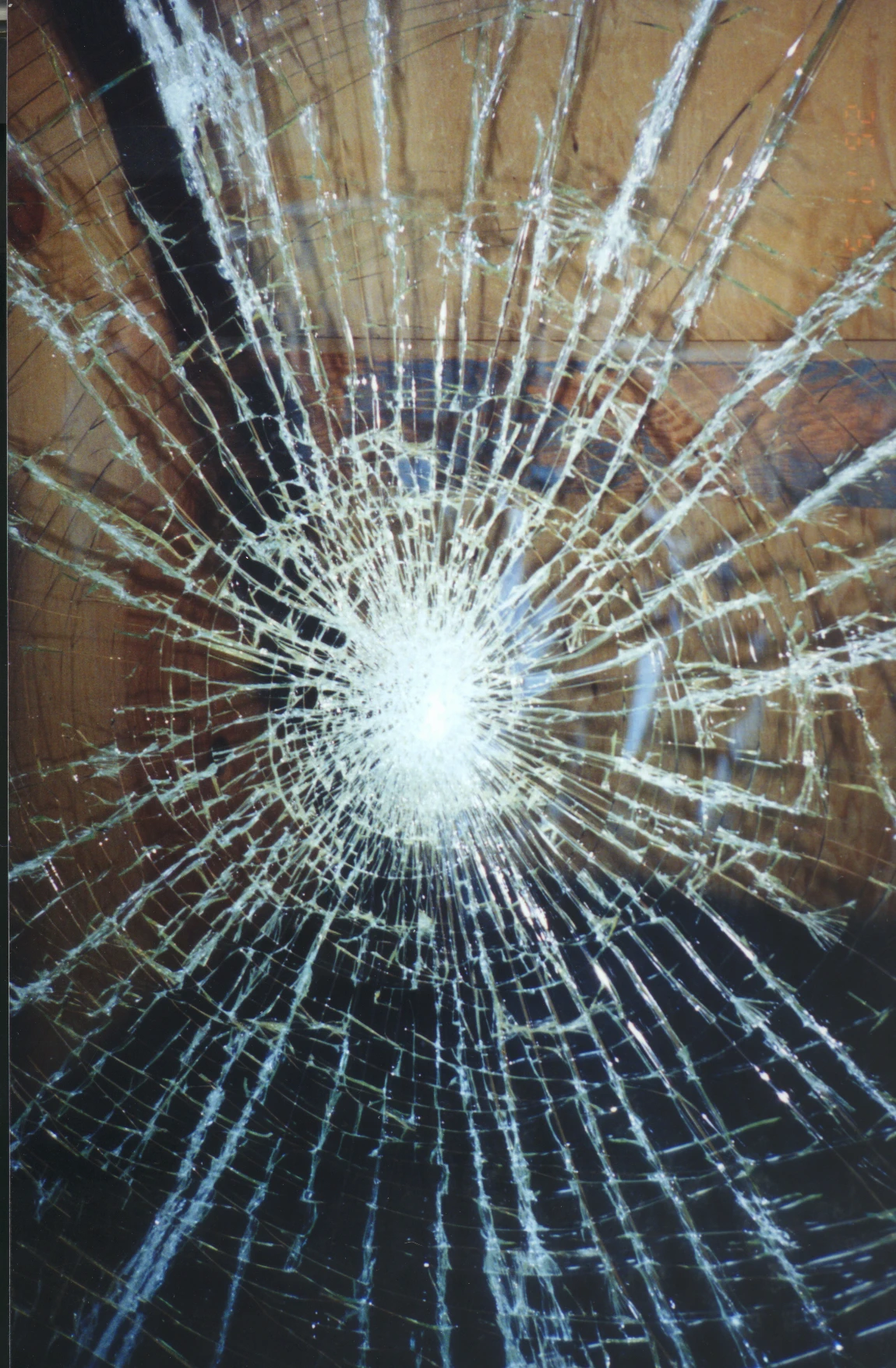
Fire Protection and Safety: Industry Discusses Opportunities and Challenges
Fire Protection and Safety: Industry Discusses Opportunities and Challenges
Date: Jan 2023
Publication: USGlass
>>
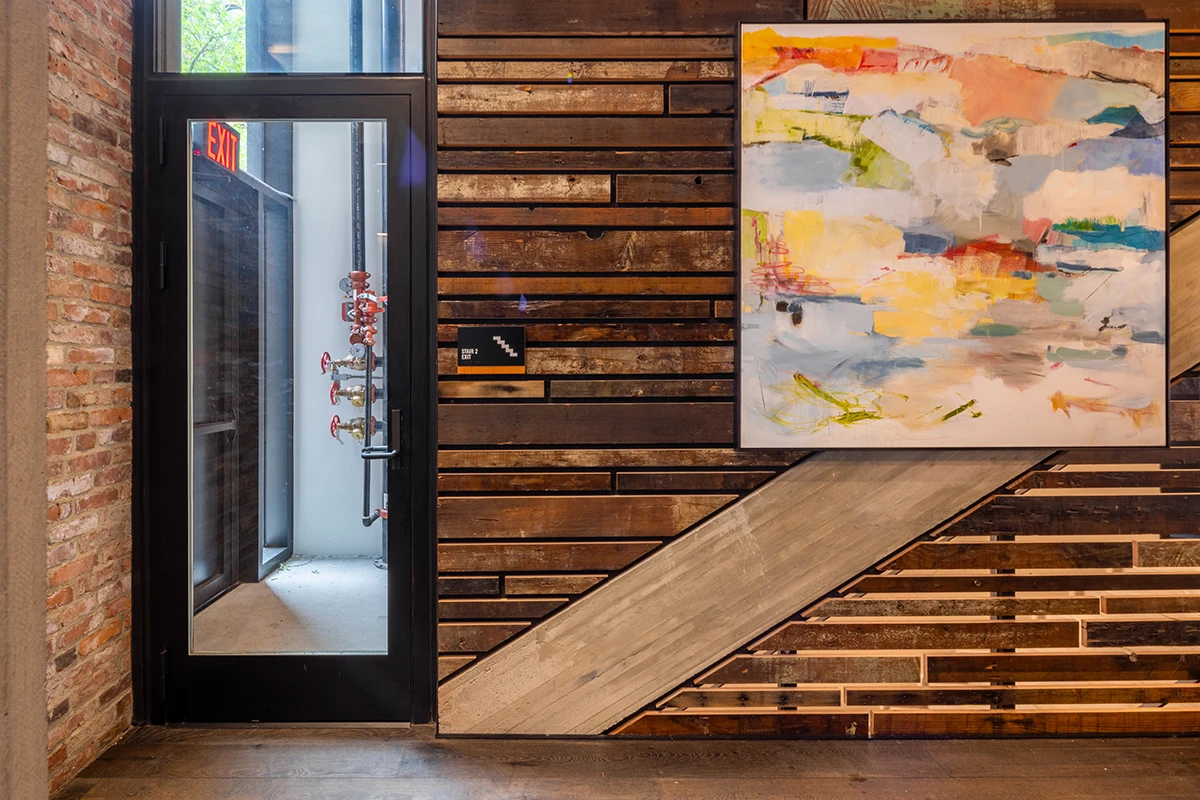
419 Occidental Avenue, Seattle
419 Occidental Avenue, Seattle
Date: Jan 2023
Publication: Retrofit
>>
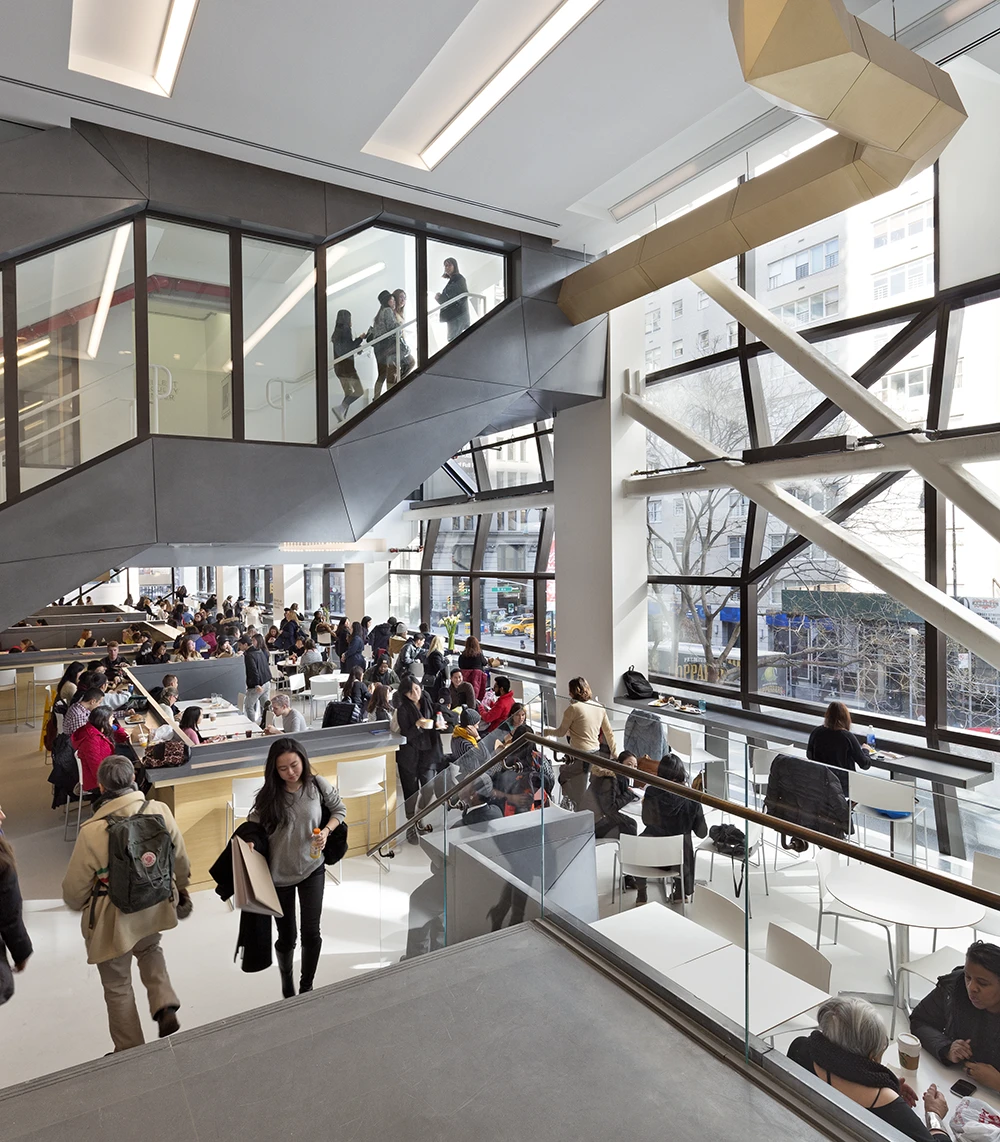
Building Design that Supports Evacuation Planning
Building Design that Supports Evacuation Planning
Date: Dec 2022
Publication: Campus Safety & Security
>>
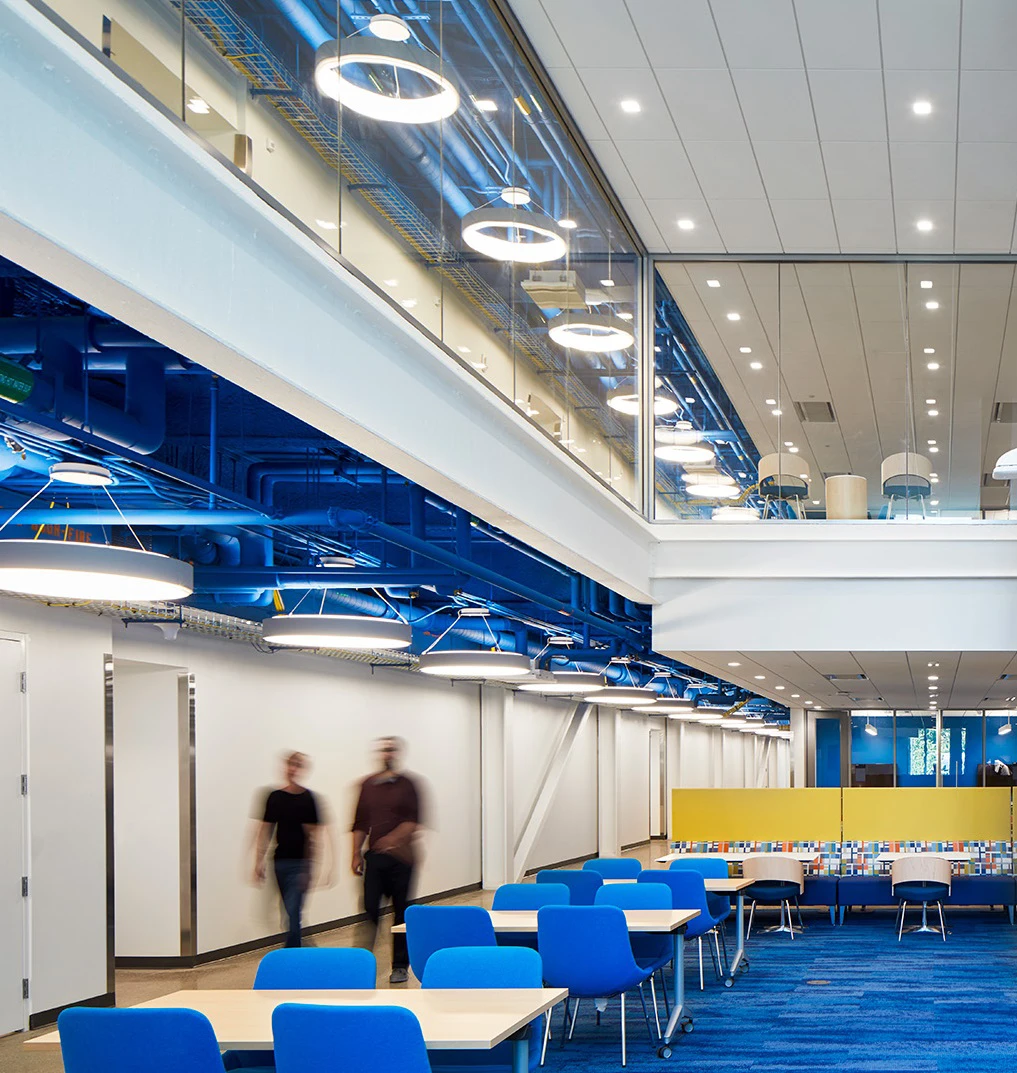
Fire-Rated Glazing Helps Achieve Design Goals at University and Beyond
Fire-Rated Glazing Helps Achieve Design Goals at University and Beyond
Date: Dec 2022
Publication: Construction Executive
>>
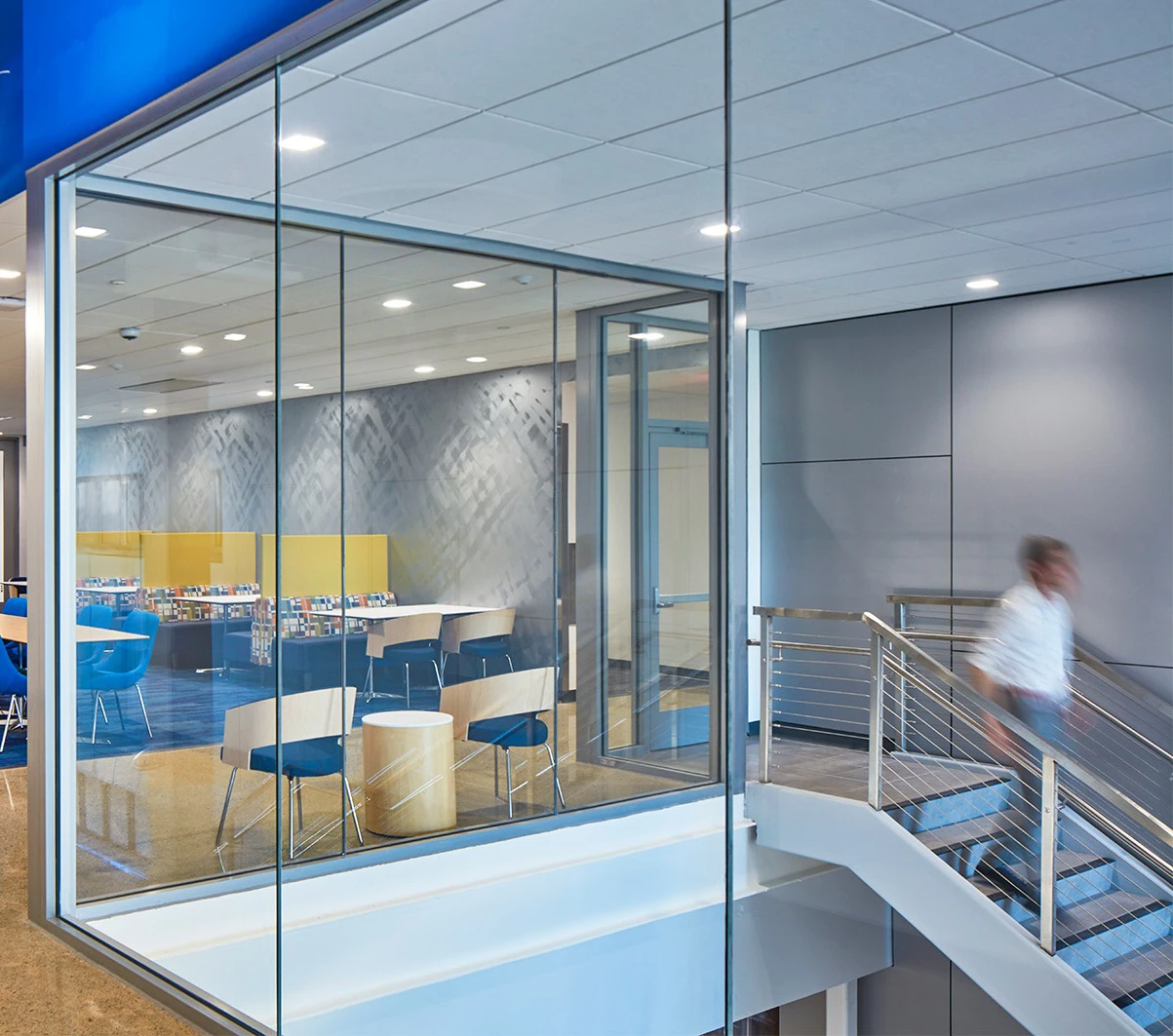
Visible STEM
Visible STEM
Date: Nov 2022
Publication: Door Security + Safety
>>
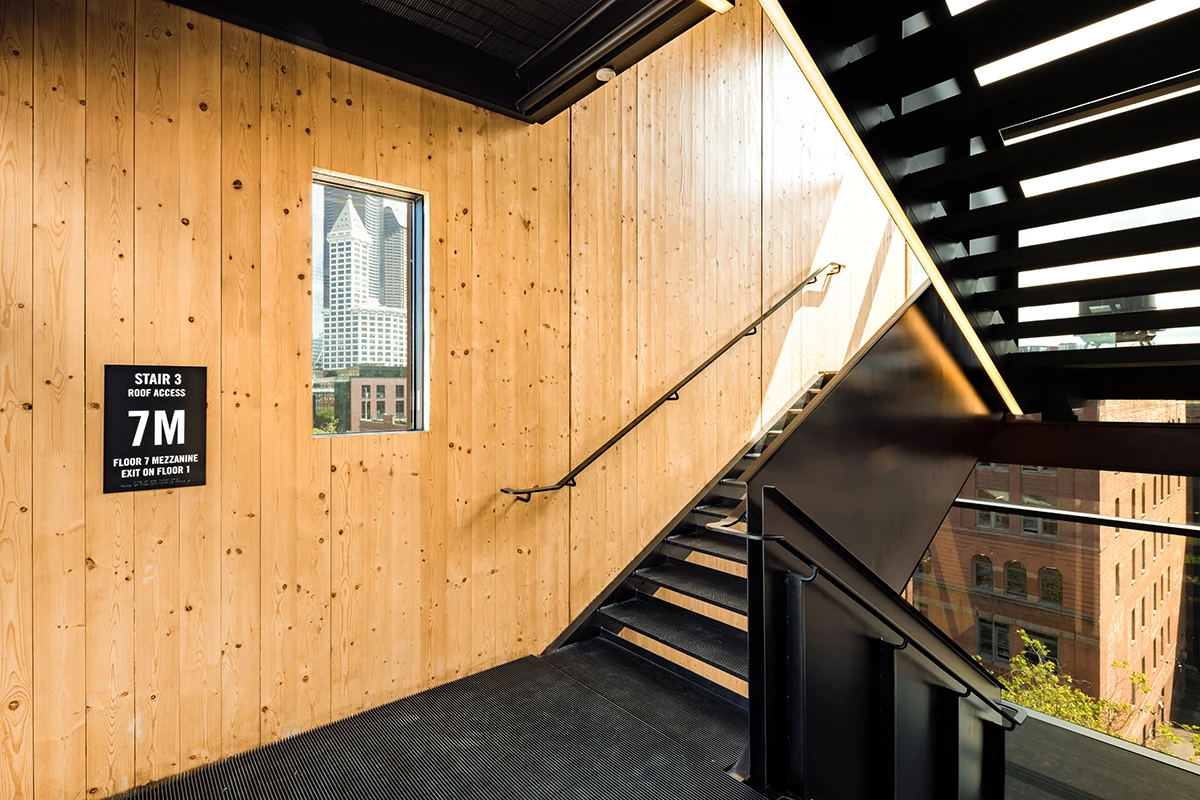
Stairwell with a View
Stairwell with a View
Date: Nov 2022
Publication: Door Security + Safety
>>
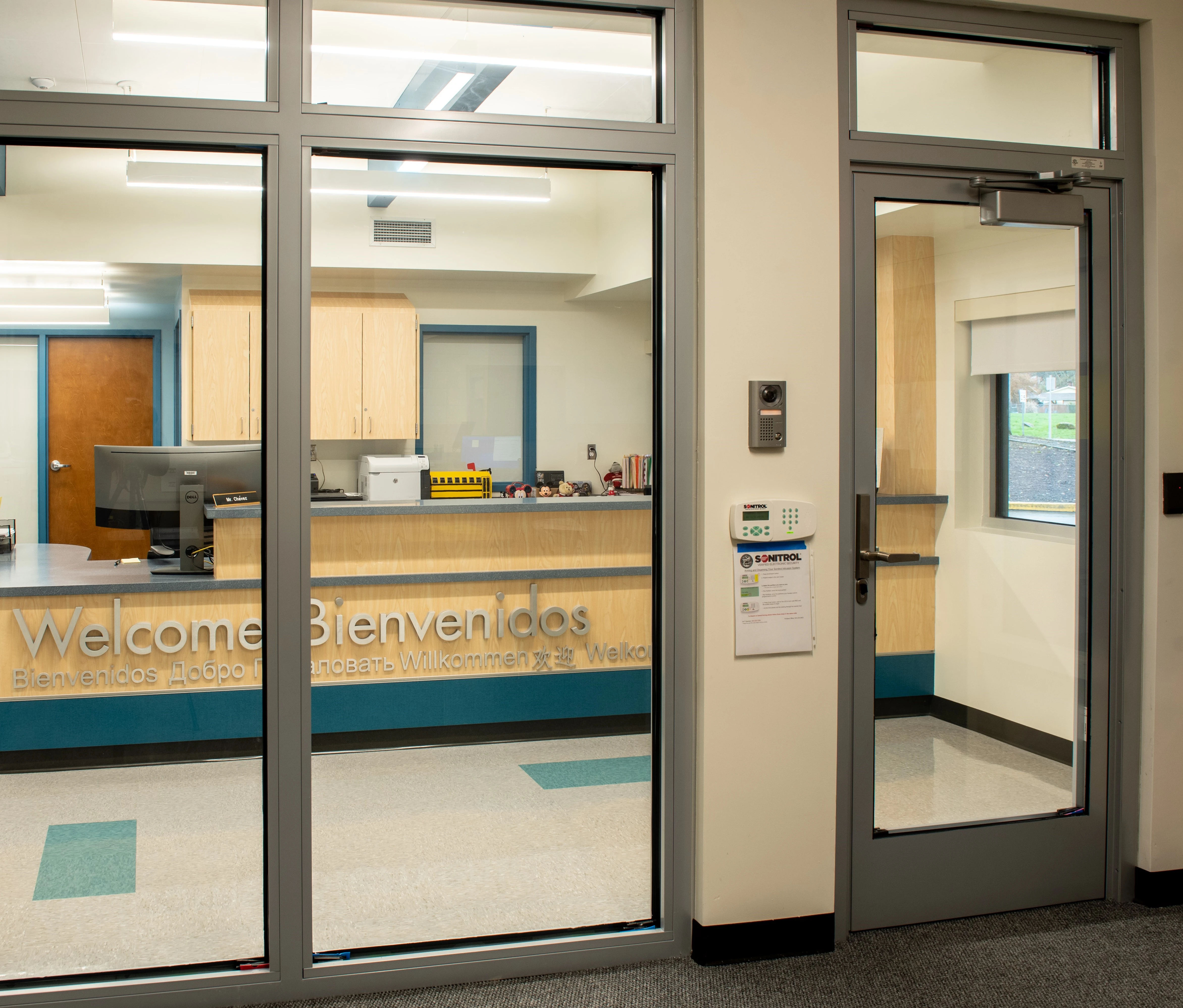
Safe & Secure With Fire-Rated Glazing
Safe & Secure With Fire-Rated Glazing
Date: Nov 2022
Publication: Facility Management
>>
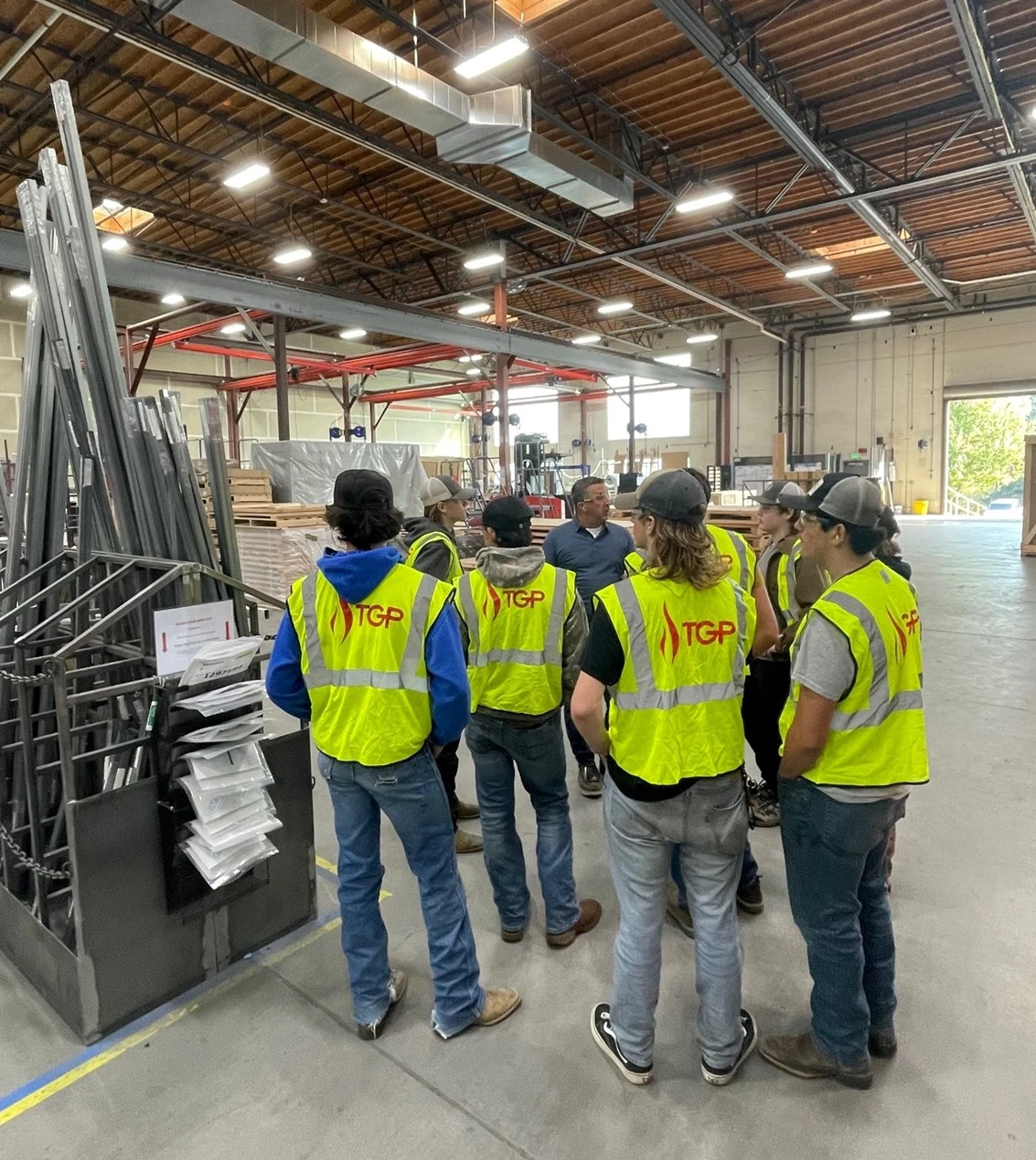
Allegion Hosts Local High School Students for Manufacturing Day
Allegion Hosts Local High School Students for Manufacturing Day
Date: Oct 2022
Publication: USGlass
>>
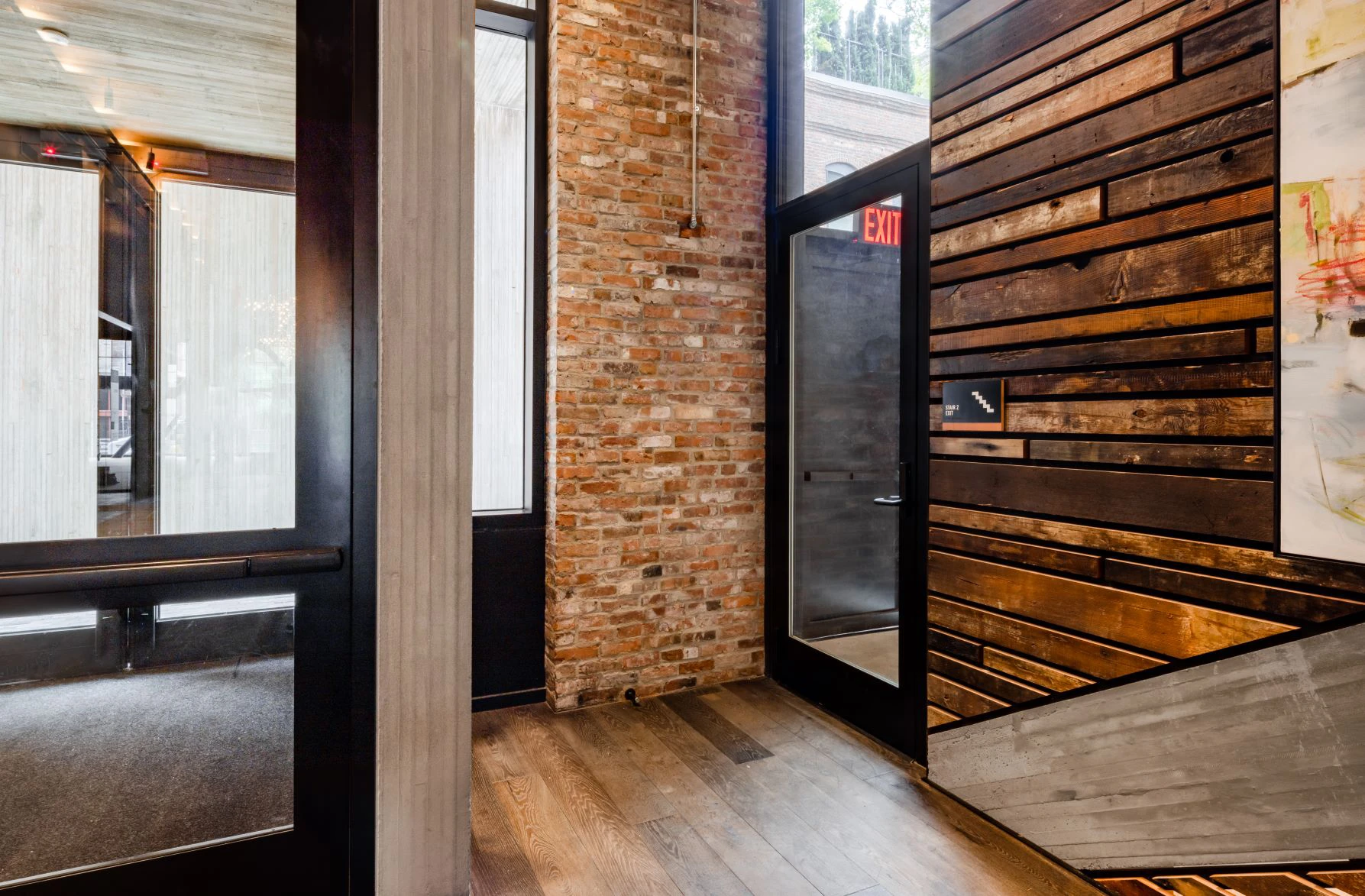
An Elevated Renovation
An Elevated Renovation
Date: Sept 2022
Publication: Architectural West
>>
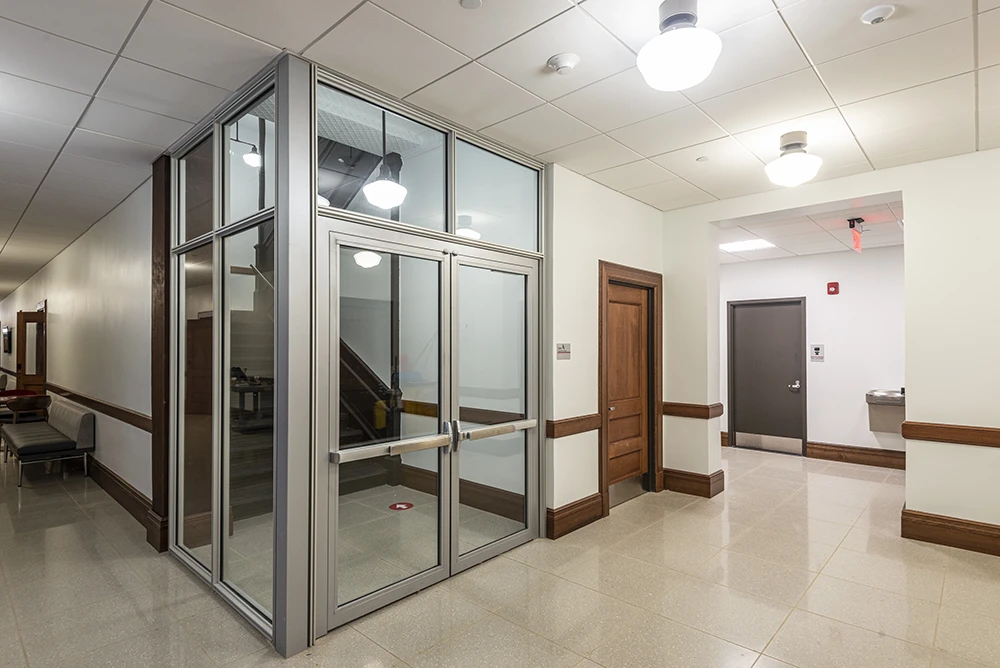
It’s All About Transparency: How fire-rated doors and frames contribute to sustainable buildings
It’s All About Transparency: How fire-rated doors and frames contribute to sustainable buildings
Date: Sept 2022
Publication: Door Security + Safety
>>
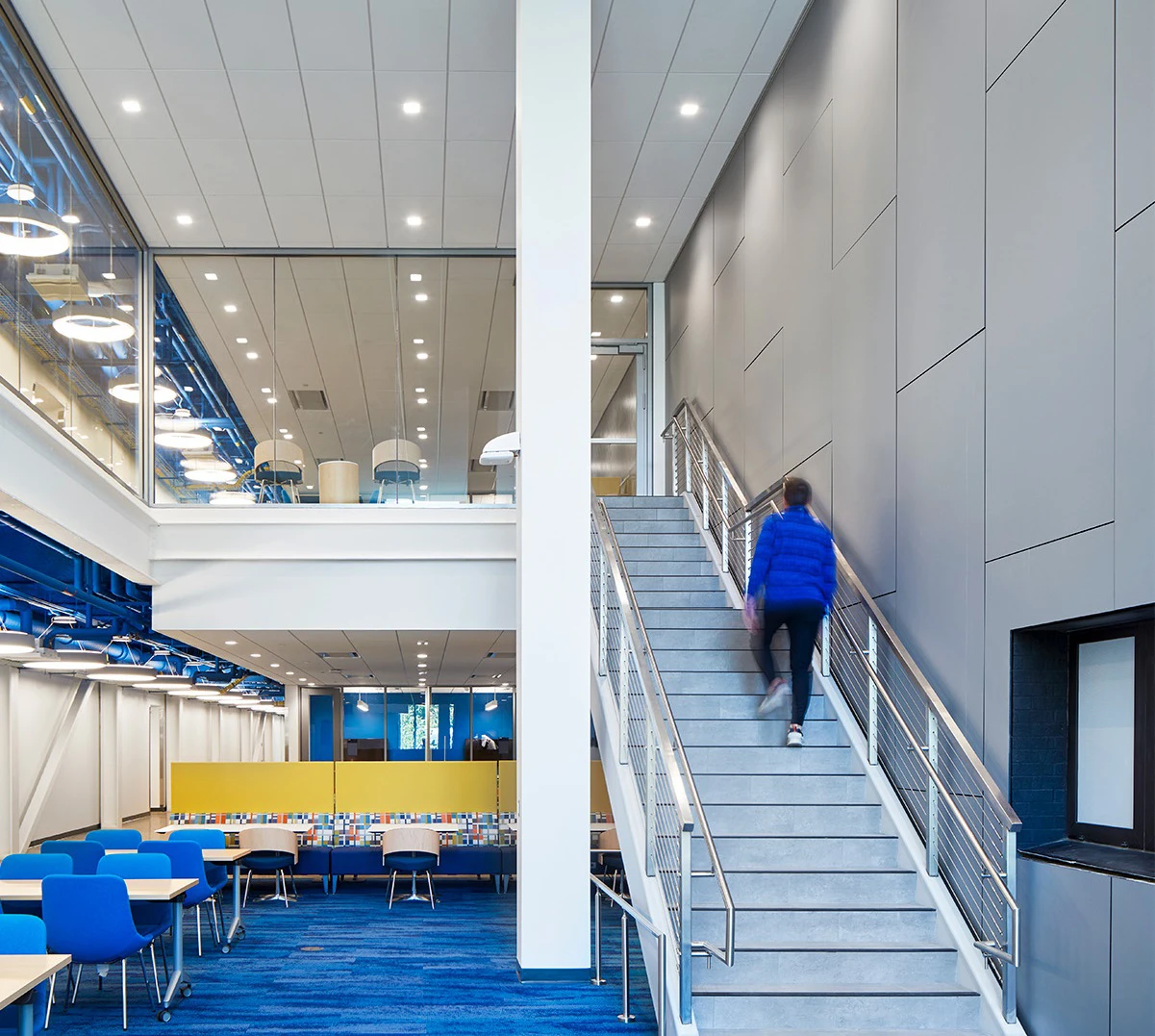
Multifunctional Fire-Rated Assemblies Satisfy Building Code and Design Intent
Multifunctional Fire-Rated Assemblies Satisfy Building Code and Design Intent
Date: Aug 2022
Publication: Building Enclosure
>>